German Logger Expands into Sawmilling With LT15
By Wood-Mizer, Canada
Countries
Ever since his childhood, Maik Retz always felt at home in the forest. Growing up two hours west of Berlin in a rural farming and forestry area, he knew he wanted to make forestry his career. His father started a business producing firewood and fencing material more than 40 years ago, and Maik started working in the business in 1994. Maik now operates the business with his brother and one other employee.
When Maik took over the business, he primarily worked as a logger in the national forests, using a newly procured forwarder, as well as producing firewood when he was not logging. Gradually, the logging business grew and they were able to upgrade their equipment. Currently they are logging 40,000 cubic metres of timber annually.
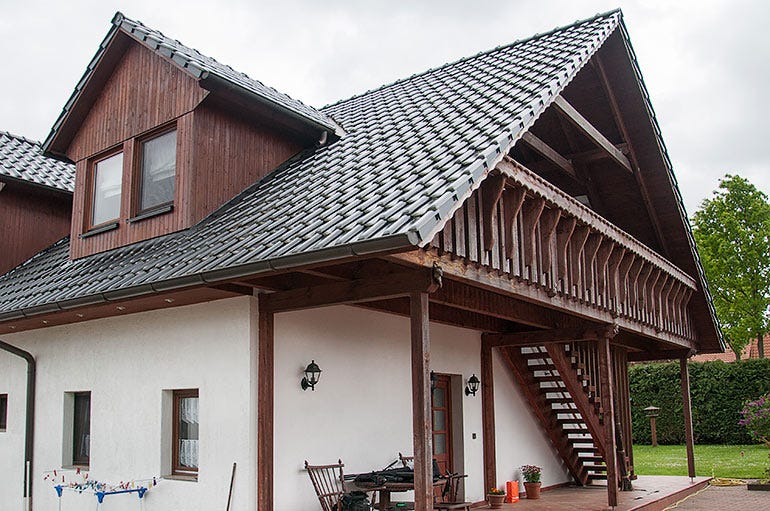
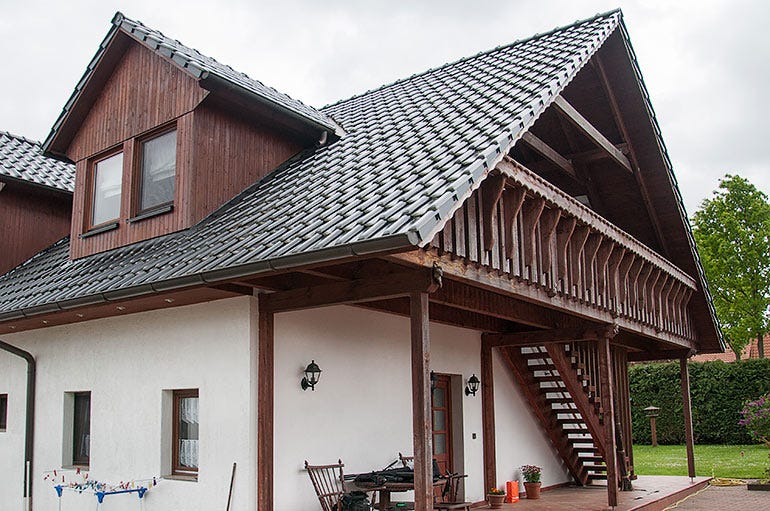
In 2000, Maik bought a Wood-Mizer LT15 sawmill to cut the timbers he needed to remodel his house. After the remodelling project was completed, Maik realised that the sawmill would be a good tool to incorporate into their logging and firewood business. The LT15 formed the basis of again producing oak beams and fencing materials for local landowners and farmers.
“The look of rustic wood with bark left on the edges is quite popular right now,” shares Maik. He focuses on producing fencing materials impossible to source from large timber yards and department stores, which creates a consistent local demand for his products.
Annually, Maik sells 7,000 oak fence posts, which keeps the LT15 sawmill busy every day. Maik estimates that when two people are working and using a forklift to assist with transporting logs and the finished beams, they can produce 2.5 metres of fencing materials per hour.
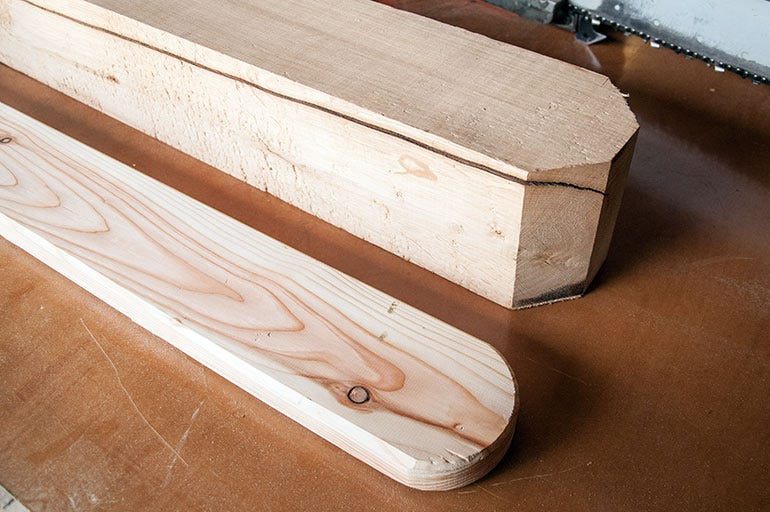
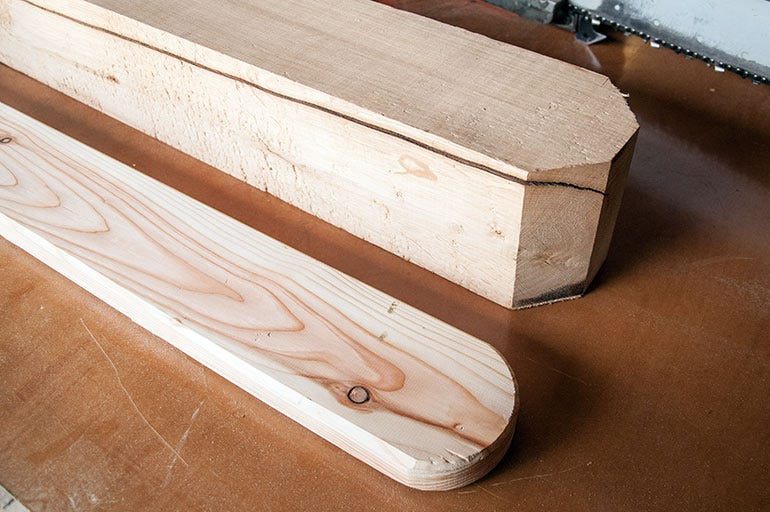
Customers include farmers, horse owners, and the Forestry department who protects new plantations of tree seedlings with stout oak fences. Homeowners near larger towns prefer to use fencing material with a finished, flat surface, instead of split rails and Maik’s LT15 creates exactly the smooth finish needed.
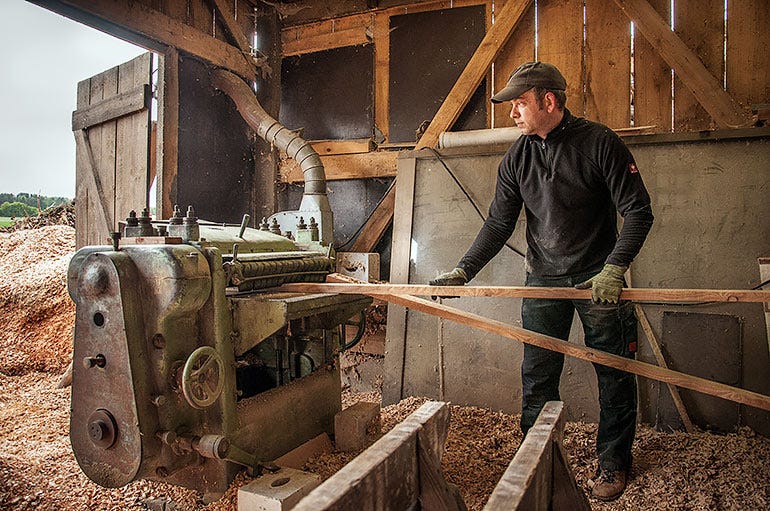
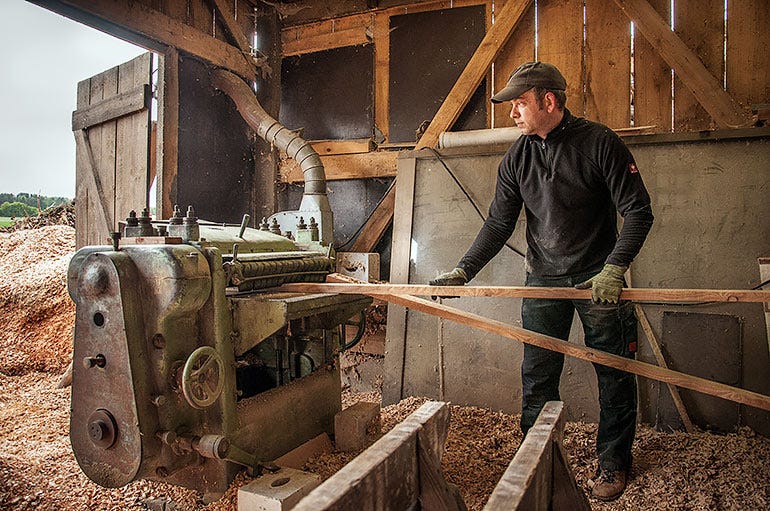
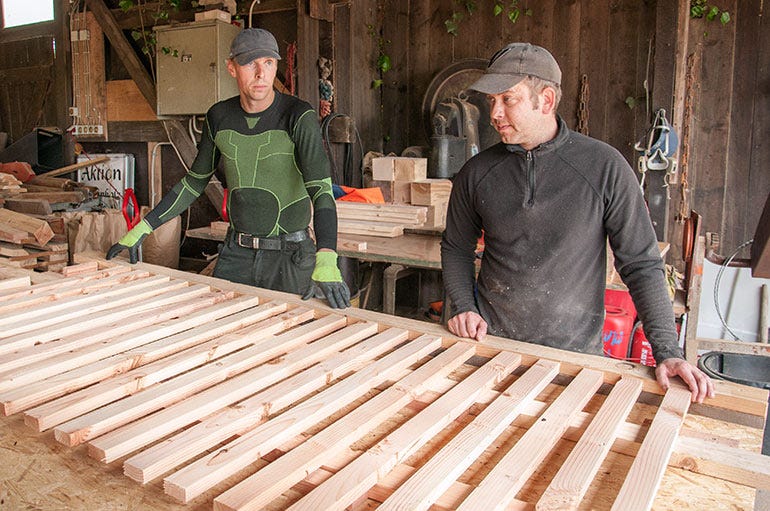
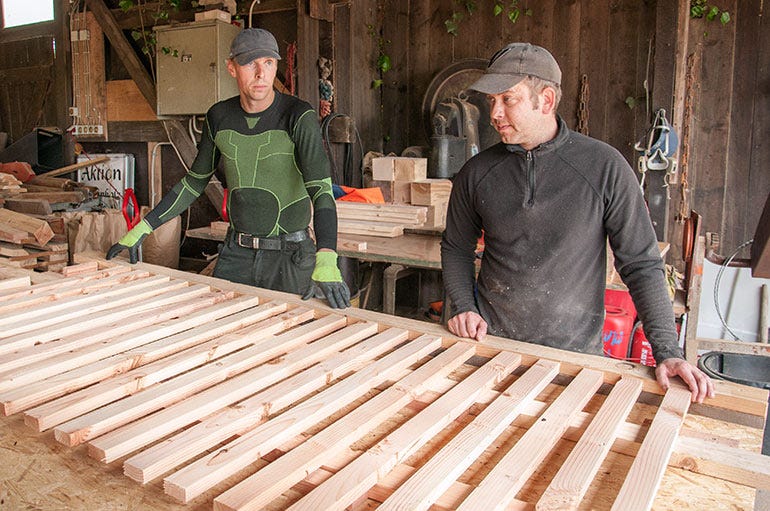
Maik likes the flexibility his business offers him to either work at the workshop producing fencing material and firewood, but then also to work alone in the middle of the forest other days.
Having different final destinations for his logs in mind, Maik is able to maximise the value of the timber he harvests. While logging, he is already mentally classifying logs and sorting them in the trailer according to their intended use.
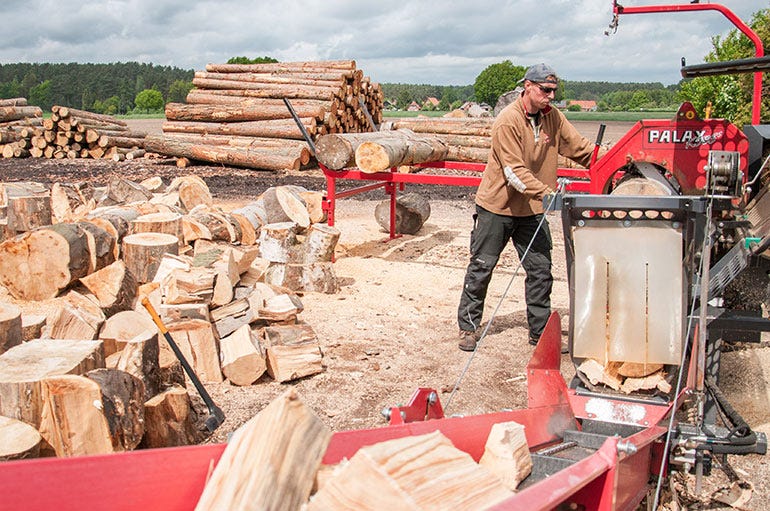
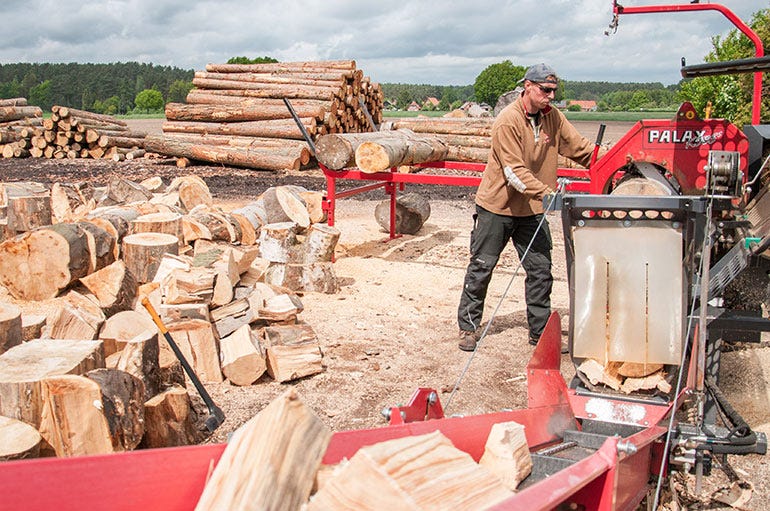
“Logs I need for the LT15 are sorted from logs intended to be sold or converted into firewood,” shares Maik. “This largely eliminates having to evaluate and sort the logs later.” High value logs are sold for good prices, others are sawn into fencing material, and the lower value logs are made into firewood. The company produces approximately 8,000 cubic metres of firewood annually.
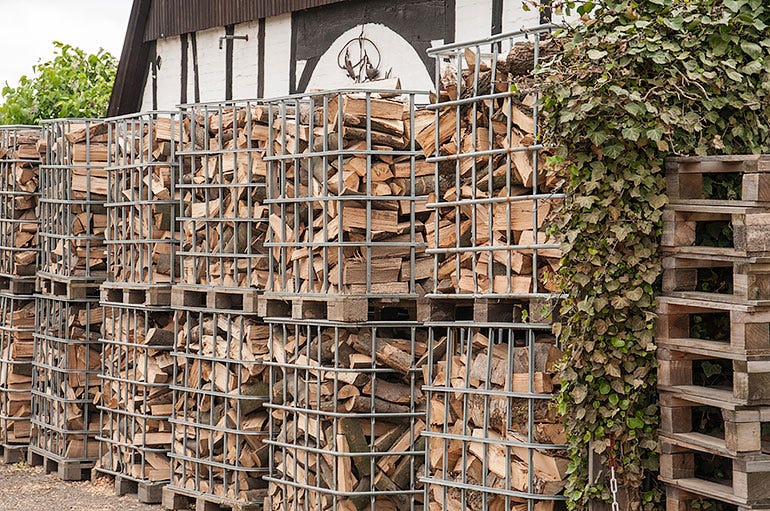
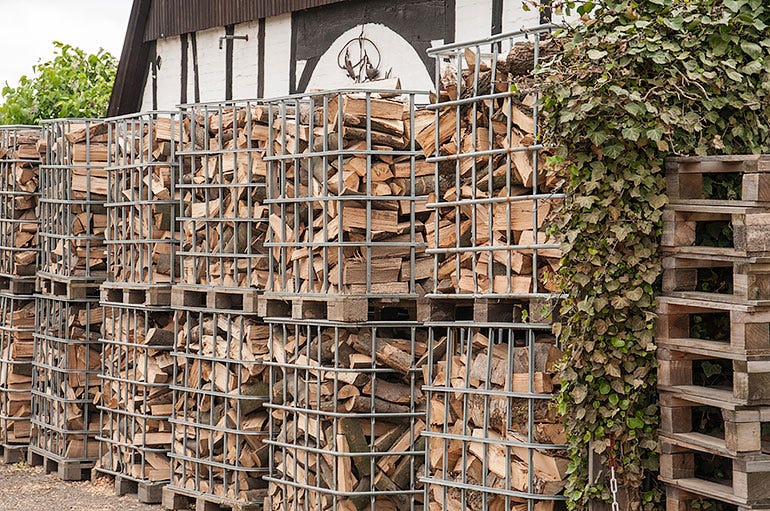
Maik is looking forward to another step in optimising the business by installing a wood waste boiler to power the central heating for his homes and business. Once the system is installed, he will be able to maximise the sawdust and wood waste he produces by using it to fuel the heating system.
For other companies looking to grow in their timber production capabilities, Maik offers this advice. “Be patient and work like wood grows – slow and persistent.”
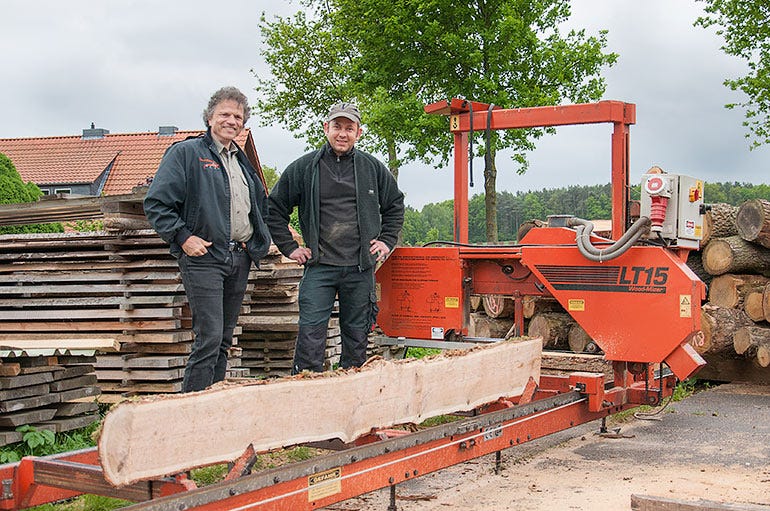
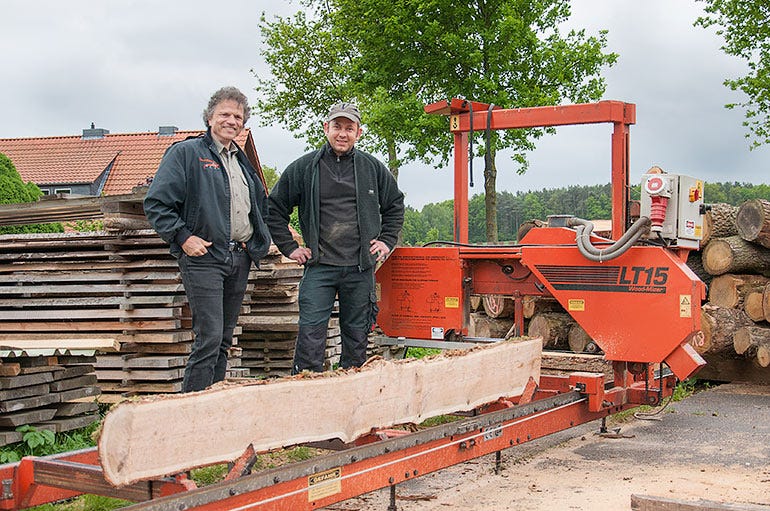
Ever since his childhood, Maik Retz always felt at home in the forest. Growing up two hours west of Berlin in a rural farming and forestry area, he knew he wanted to make forestry his career. His father started a business producing firewood and fencing material more than 40 years ago, and Maik started working in the business in 1994. Maik now operates the business with his brother and one other employee.
When Maik took over the business, he primarily worked as a logger in the national forests, using a newly procured forwarder, as well as producing firewood when he was not logging. Gradually, the logging business grew and they were able to upgrade their equipment. Currently they are logging 40,000 cubic metres of timber annually.
In 2000, Maik bought a Wood-Mizer LT15 sawmill to cut the timbers he needed to remodel his house. After the remodelling project was completed, Maik realised that the sawmill would be a good tool to incorporate into their logging and firewood business. The LT15 formed the basis of again producing oak beams and fencing materials for local landowners and farmers.
“The look of rustic wood with bark left on the edges is quite popular right now,” shares Maik. He focuses on producing fencing materials impossible to source from large timber yards and department stores, which creates a consistent local demand for his products.
Annually, Maik sells 7,000 oak fence posts, which keeps the LT15 sawmill busy every day. Maik estimates that when two people are working and using a forklift to assist with transporting logs and the finished beams, they can produce 2.5 metres of fencing materials per hour.