Livengood Pallets Rebuilds After Fire with Wood-Mizer Pallet Hawg Equipment
By Chase Warner, Wood-Mizer
Countries
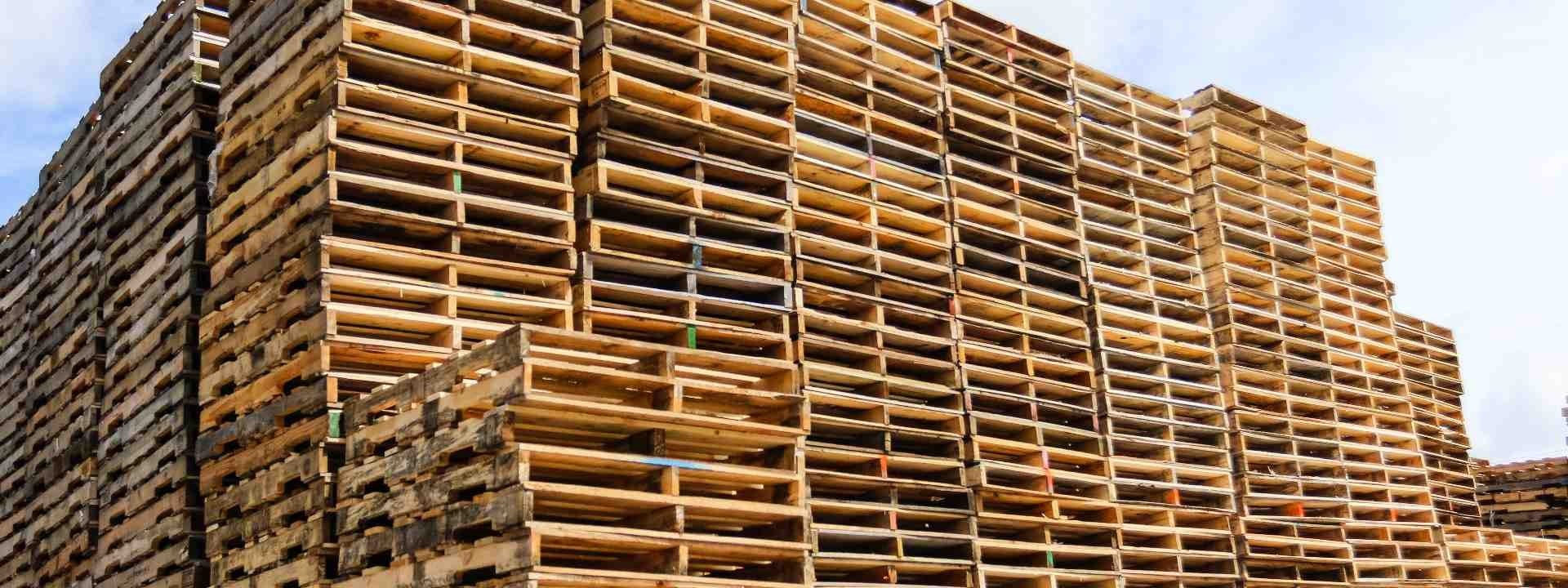
Located in Frankfort, Indiana, the 35-year-old family owned Livengood Pallet Service has found success by changing with market demands and overcoming tragedy. After deciding to primarily focus on recycling pallets in order to remain profitable, the company suffered a devasting fire in 2017 which resulted in a complete loss for the business. Only a few years removed from the fire, Livengood Pallets has rebuilt their operation around 8 full-time employees, a new production facility, and three Wood-Mizer Pallet Hawg® pallet dismantlers as the backbone of their operation.
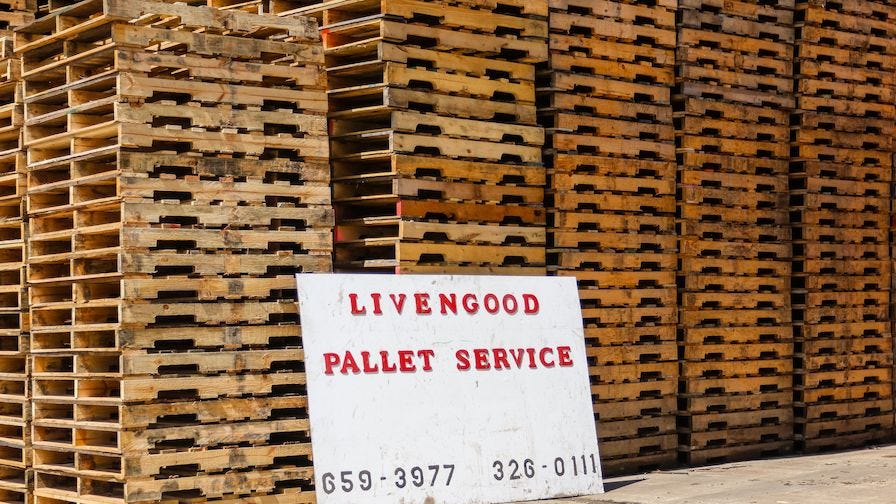
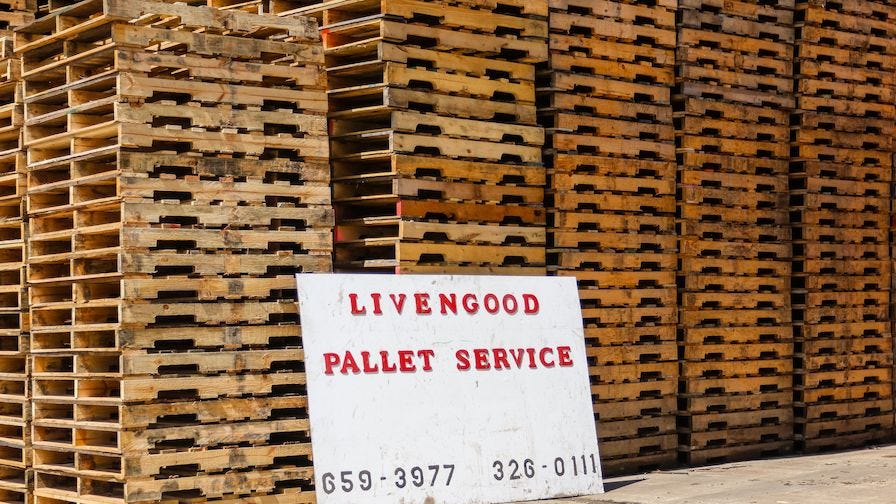
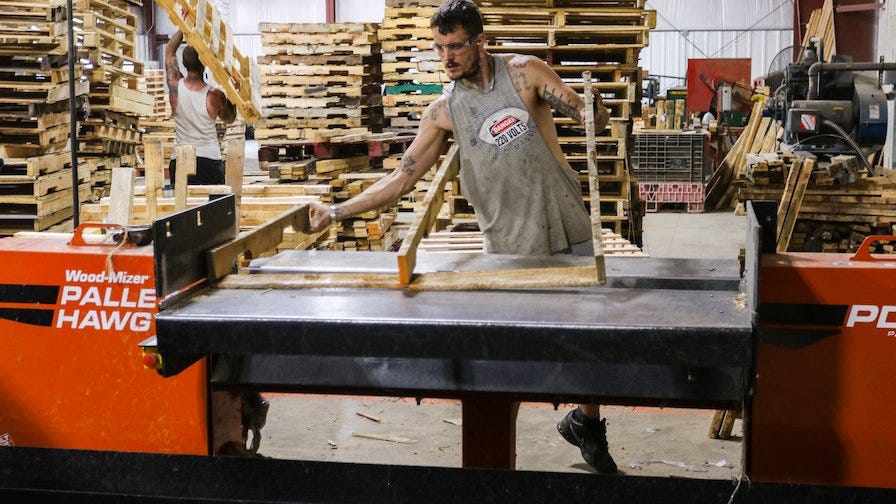
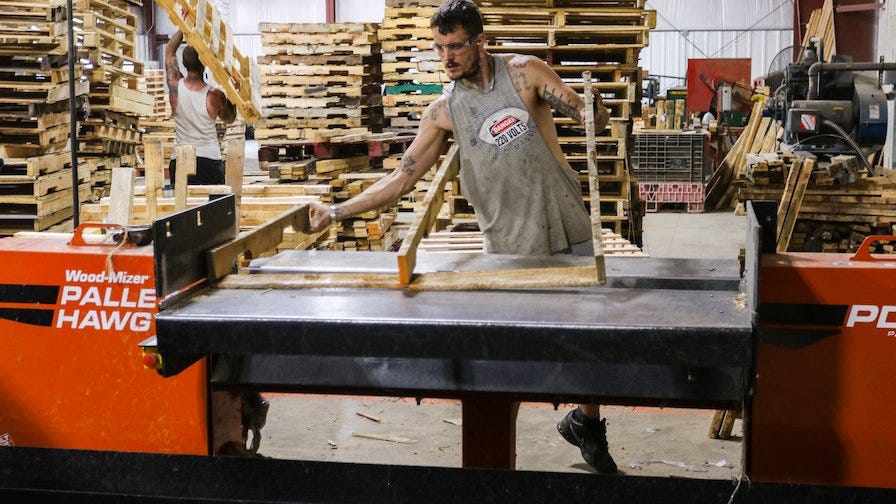
Livengood Pallet Service was started in 1984 by owner Jerry Livengood when he began transporting and selling pallets with a pickup truck and using his parents’ backyard to store his inventory. “At that time you could get paid to haul pallets off,” said Jerry. “Now everybody knows they’re worth money.” The pallet recycling operation continued to grow so they decided to begin manufacturing new pallets after investing in a Wood-Mizer LT40 hydraulic portable sawmill and a 2-head horizontal resaw. In addition to recycling material, the company sawed round logs into 4-sided cants on the sawmill and then cut cants into stringers and deck boards on the resaw. The boards from the resaw were then sent to a pallet notcher or trim saw and assembled into a new pallet.
Livengood Pallets continued recycling and manufacturing new pallets until market changes caused the company to revisit their business model. In the early 2010s, Jerry Livengood and his son Derek decided the best move for the company was to focus solely on recycling pallets and building combo pallets with both new and recycled material. “We got away from the core wars and started concentrating on uncommon sized pallets to dismantle and build the combo pallets,” said Jerry. “I wish we started building combos way before we did.”
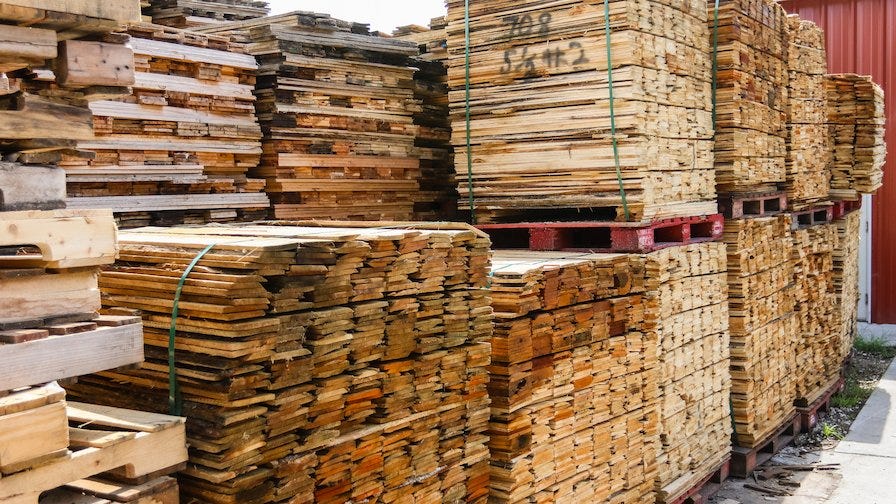
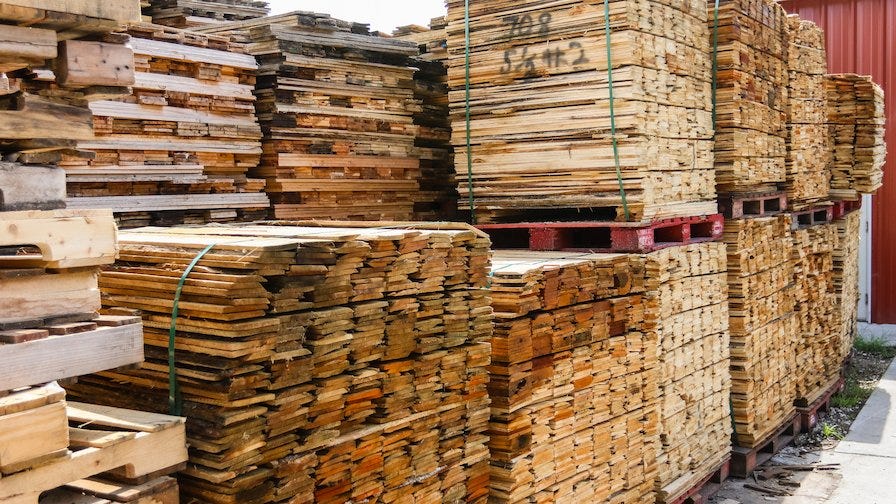
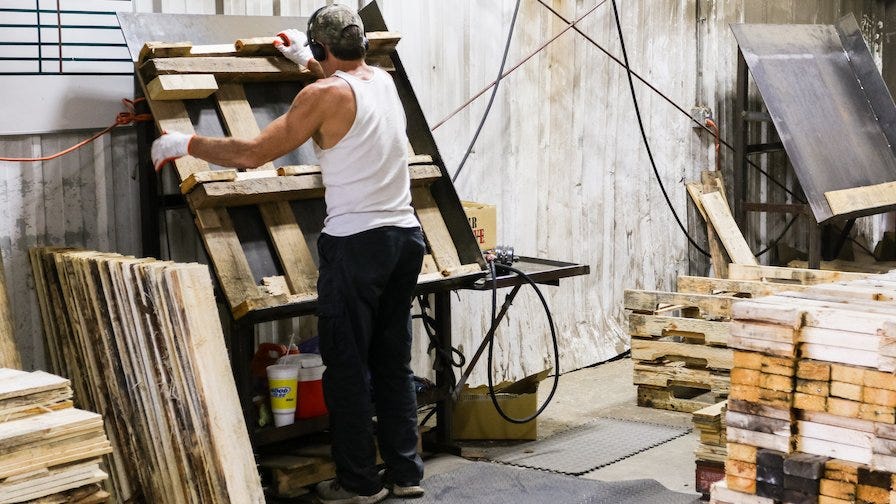
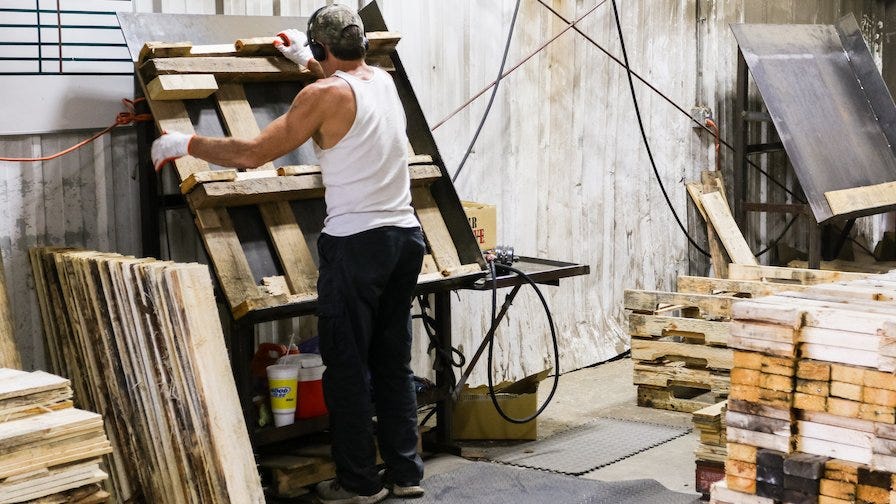
Just weeks before Christmas in 2017, Livengood Pallets suffered a fire that burned their entire operation including a 6,000 square foot facility, pallet recycling equipment, and a large inventory of lumber. With the pallet plant shutdown, their employees found other jobs in order to make ends meet. During the next few months, Jerry and Derek rebuilt a new production facility and invested in a range of pallet recycling and manufacturing equipment including three Wood-Mizer Pallet Hawg dismantlers, trim saw, pallet notcher, and a semi-automated pallet assembly machine to get the business up and running again. “After the fire all my employees came back to work for us even though they had other jobs at the time,” said Jerry.
Today, the company operates with 8 full-time employees that do a range of jobs including transportation, machine operation, and material handling. Together, the team dismantles on average more than 700 pallets per day and manufactures a semi-load of 546 pallets per day. “Our pallets going out have 12 boards, and a lot of our pallets coming in only have 7 boards so that’s where the difference is to keep our daily flow,” said Jerry.
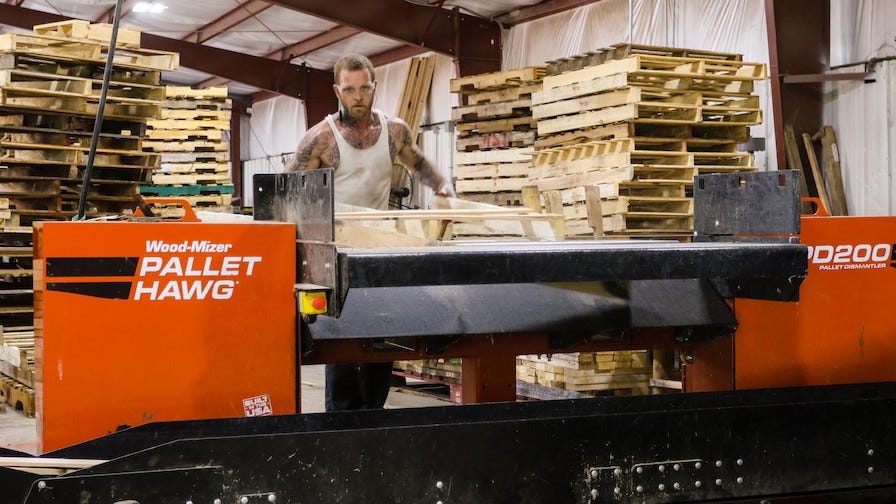
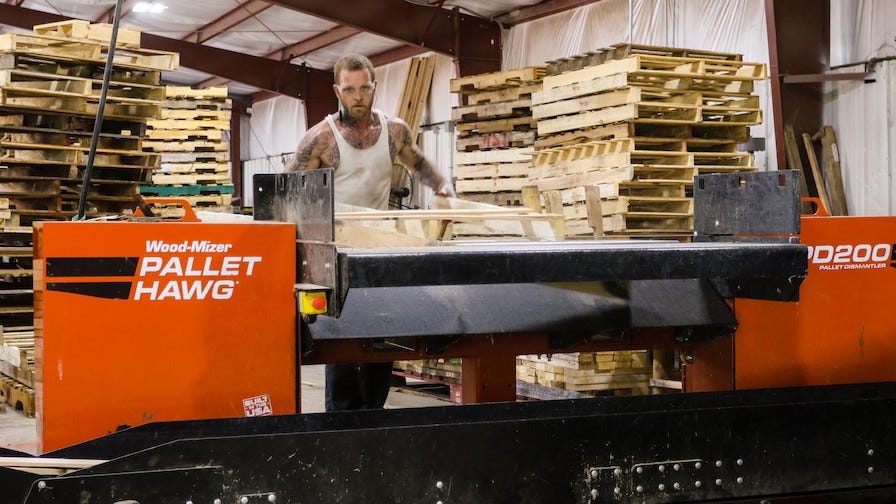
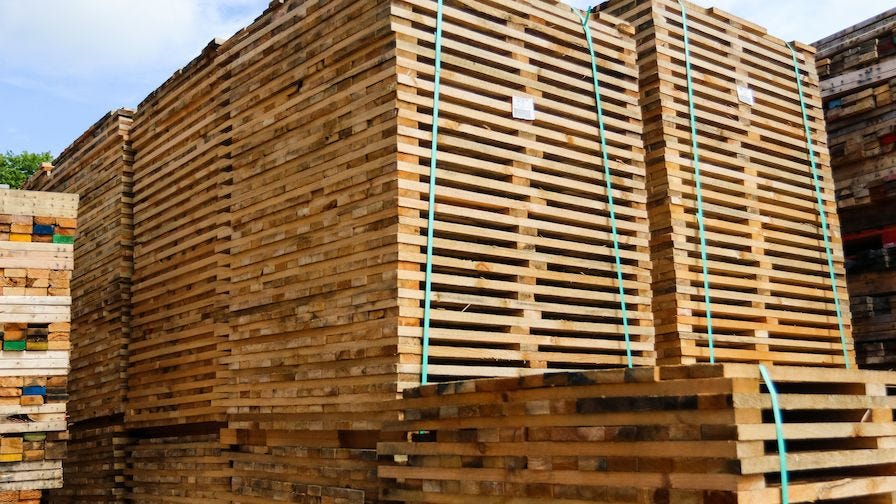
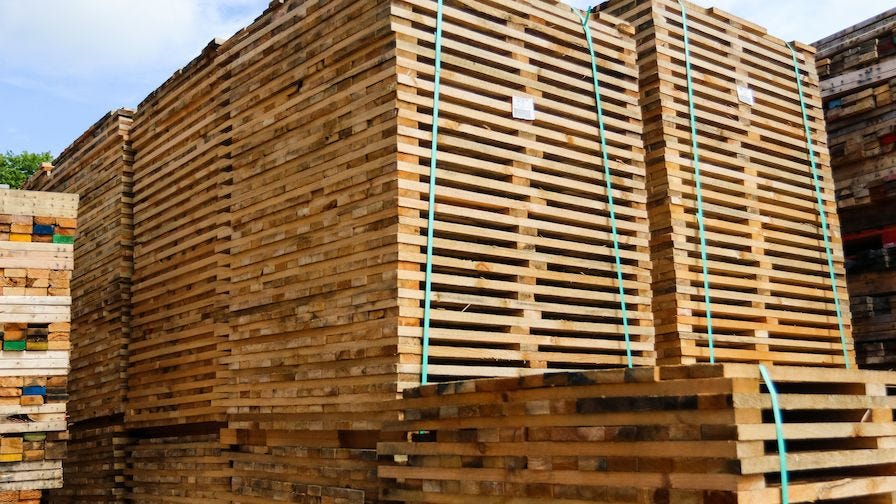
The centerpiece of the operation are two Wood-Mizer Pallet Hawg pallet dismantlers with a center drop and conveyor that automatically moves dismantled boards to the trim saw. “The Pallet Hawgs have very minimal maintenance and don’t lose power in the cut like the other machines we’ve used,” said Jerry. Each dismantler is operated by one person and dismantles upwards of 350 pallets per day per person. Compared to previous two-person dismantlers the company has used, the Pallet Hawg and conveyor system is achieving the same production with half of the operators. “One-man operation has been a lot better with less labor without less production,” said Jerry. “The conveyor system takes the lumber right to the trim saw so you don’t have to off load it. That’s one reason we went away from the two-man operation.”
Approximately 90% of pallets are sent to the dismantling line with two Pallet Hawgs and conveyor system while the remaining 10% are sent to a third Pallet Hawg dismantler with a rear drop and adjustable table height. With the pneumatic table lift, larger pallets from 8’ to 16’, pallets with bottom boards or solid decks, block pallets, and other specialty pallets are dismantled without difficulty. Having the third Pallet Hawg allows the flexibility to dismantle uncommon sized pallets without disrupting the production flow of common sized pallets on the first dismantling line. Due to lower RPM of each Pallet Hawg dismantler, Livengood Pallets has also experienced up to double the blade life compared to previous dismantlers they’ve ran. “A lot of the blade life depends on the type of pallets and operators, but we have a blade on right now that has six days on it,” said Jerry. “Three to five days is average, depending on the type of pallets and nails. With the previous machines we were lucky to get two days of blade life as the RPMs were twice as fast at 4500 RPM versus 2200 RPM of the Pallet Hawgs.”
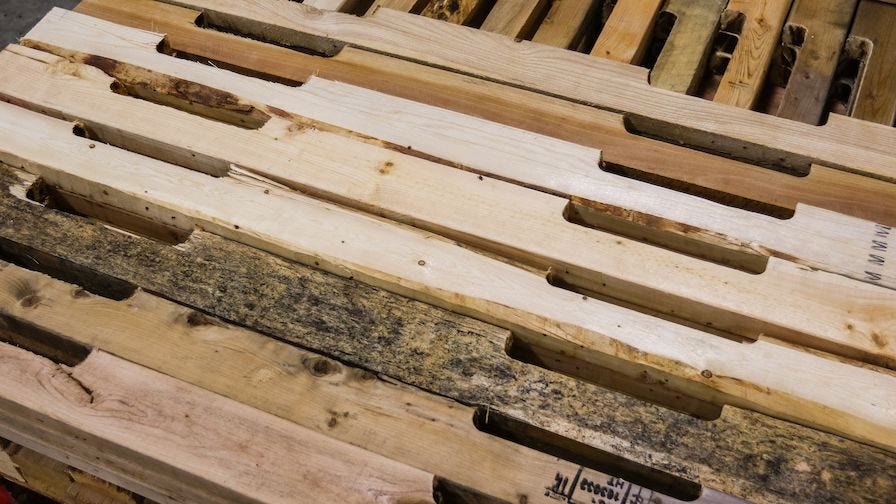
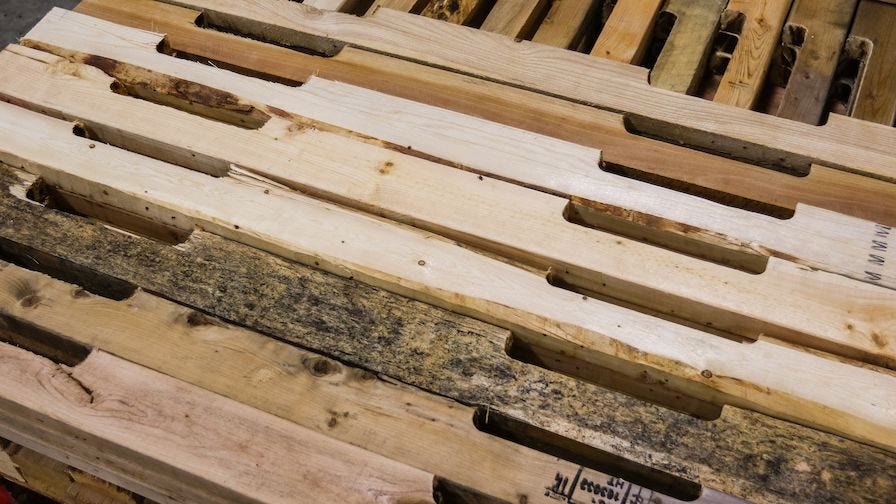
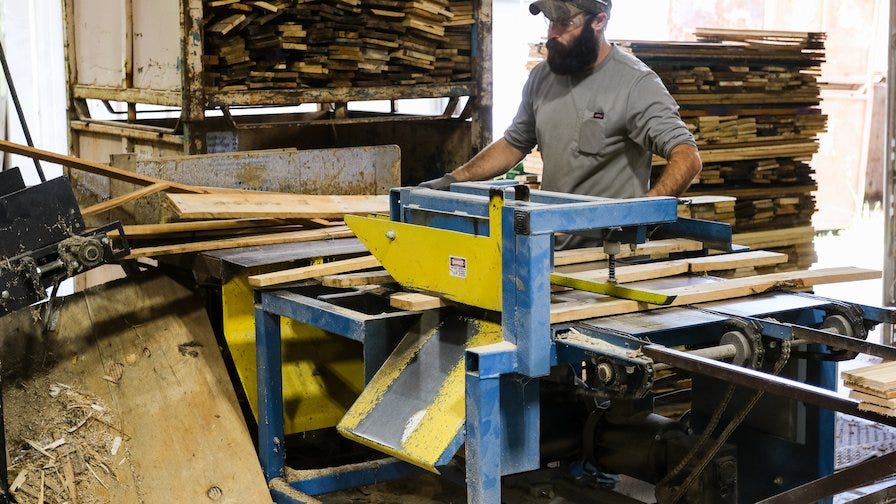
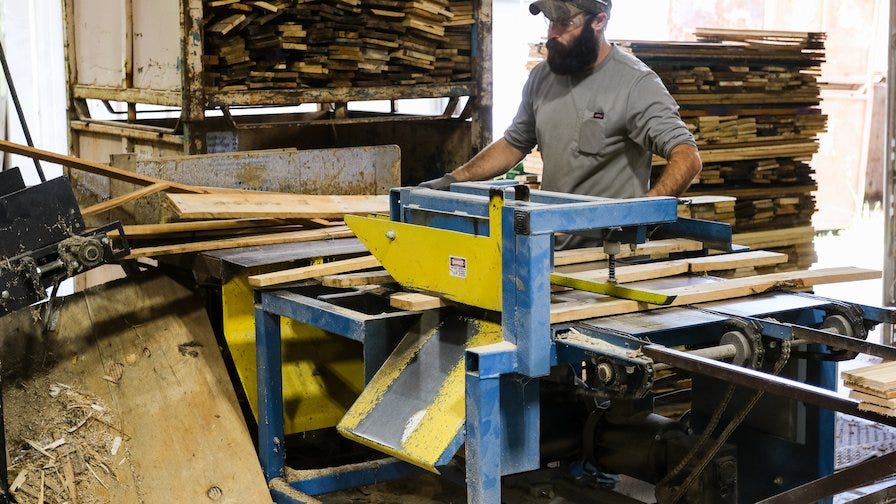
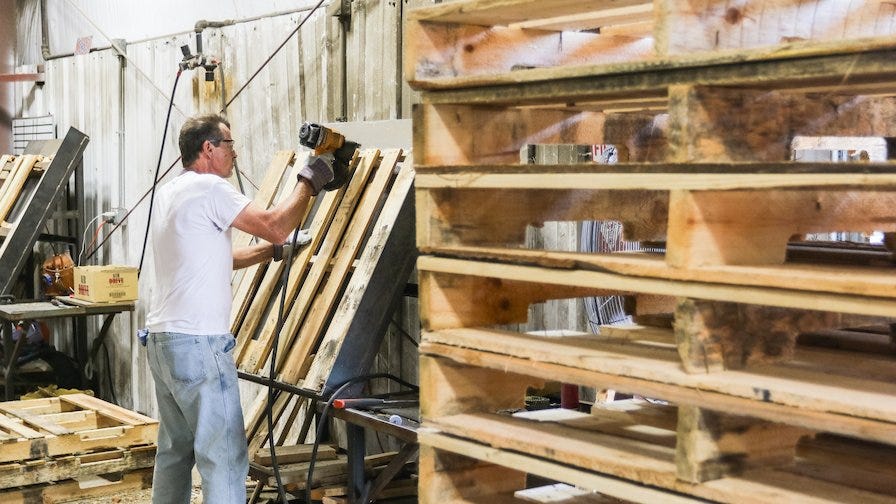
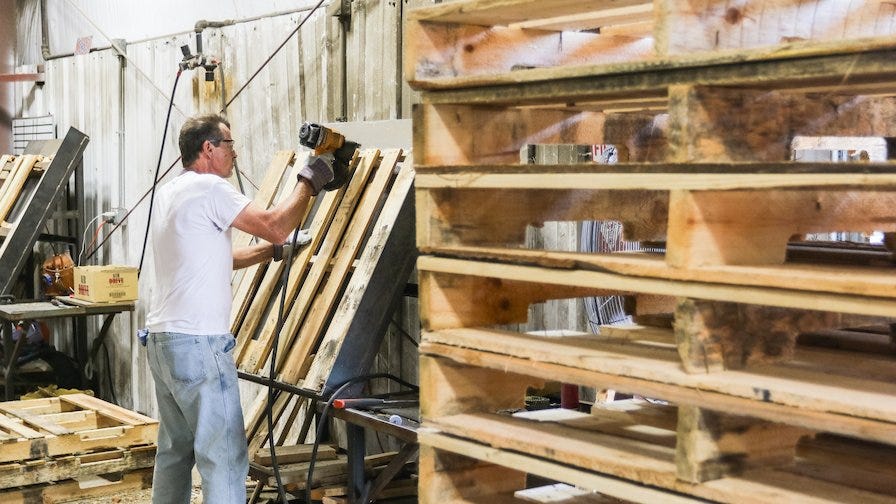
After pallets are dismantled at one of the two lines, the deck boards are cut to length at the trim saw and stringers are notched at the pallet notcher. Finished deck boards and stringers are either stored in inventory or sent directly to the pallet assembly stations. “Our main pallet is the 48 inch by 40 inch GMA combo pallet which is primarily all we build,” said Jerry. “We try not to dismantle boards shorter than 36 inches, but when we do have shorter stock we generally build a 24 inch by 12 foot pallet or a custom-size to complete an order.”
By building relationships with local brokers as well as clients in the automobile and food storage industry, Livengood Pallets has standing orders which has helped with maintaining production flow. “We get most of our orders on Thursday and Friday for the following week so I can plan accordingly,” said Jerry. “We don’t have many last minute orders which has helped with our production planning.” For the future, Livengood Pallets has positioned themselves for continued growth and success in the pallet industry. “I owe a great deal of gratitude and a big thank you to our employees for the comeback of Livengood Pallet Service,” said Jerry.
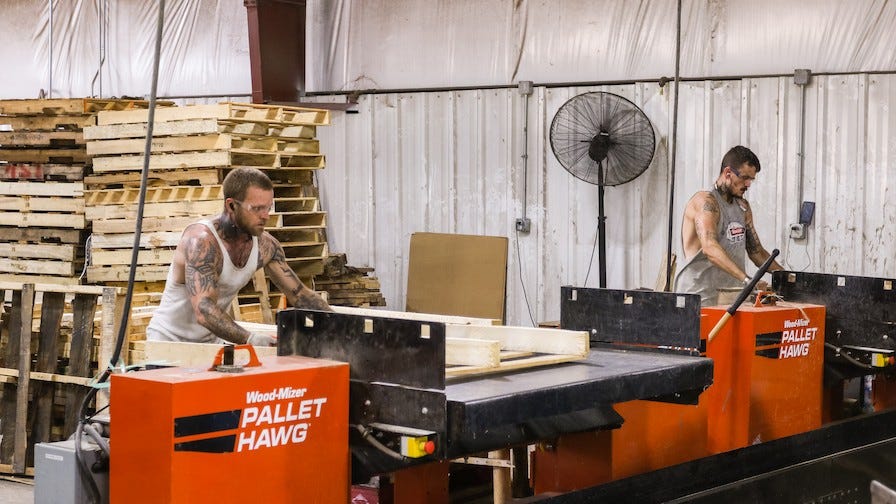
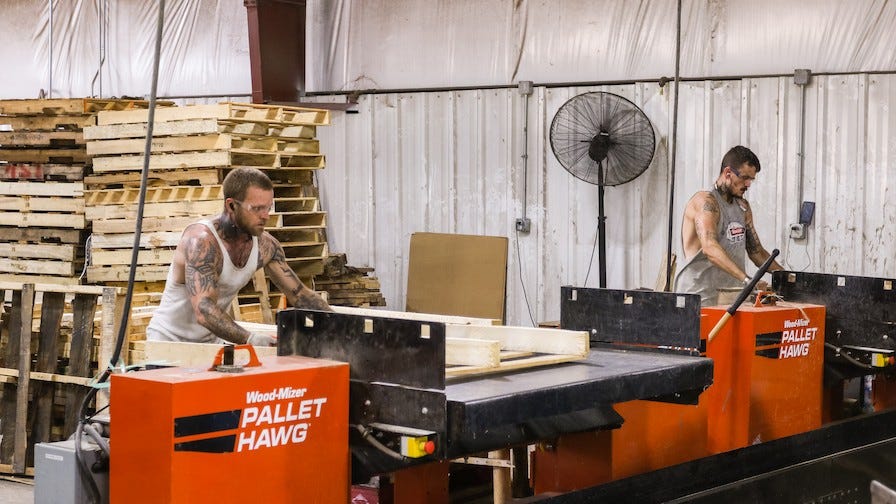
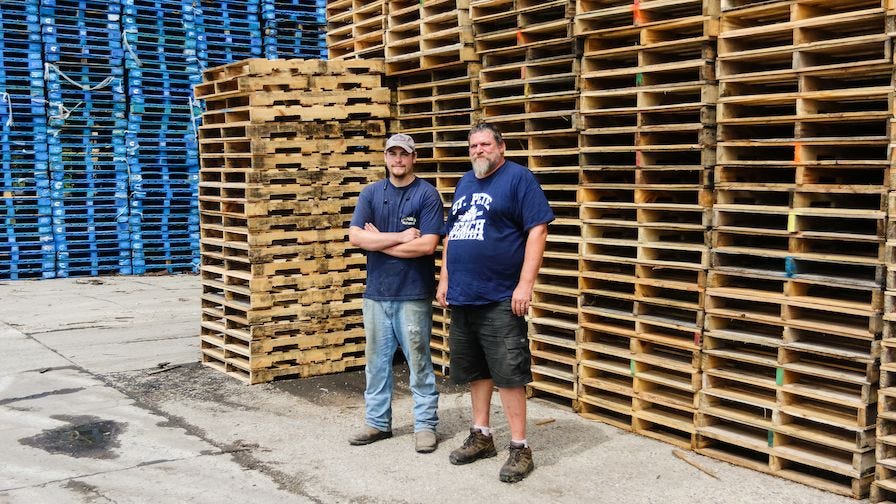
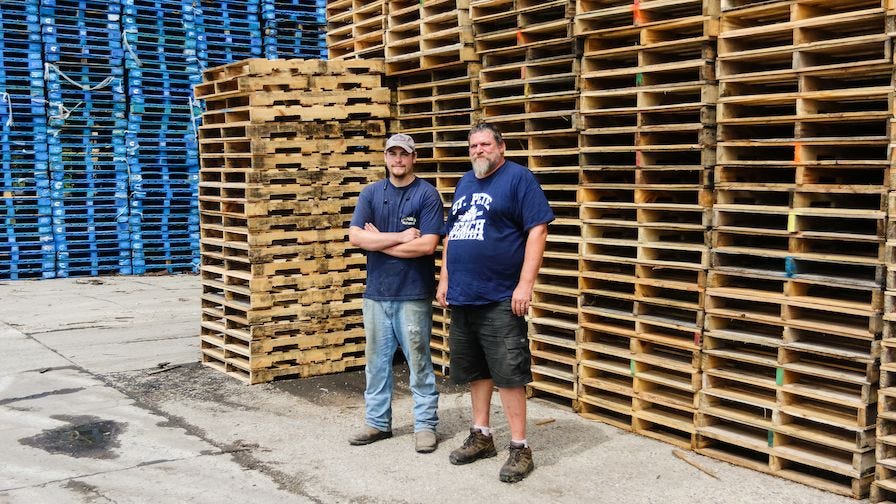
Located in Frankfort, Indiana, the 35-year-old family owned Livengood Pallet Service has found success by changing with market demands and overcoming tragedy. After deciding to primarily focus on recycling pallets in order to remain profitable, the company suffered a devasting fire in 2017 which resulted in a complete loss for the business. Only a few years removed from the fire, Livengood Pallets has rebuilt their operation around 8 full-time employees, a new production facility, and three Wood-Mizer Pallet Hawg® pallet dismantlers as the backbone of their operation.
Livengood Pallet Service was started in 1984 by owner Jerry Livengood when he began transporting and selling pallets with a pickup truck and using his parents’ backyard to store his inventory. “At that time you could get paid to haul pallets off,” said Jerry. “Now everybody knows they’re worth money.” The pallet recycling operation continued to grow so they decided to begin manufacturing new pallets after investing in a Wood-Mizer LT40 hydraulic portable sawmill and a 2-head horizontal resaw. In addition to recycling material, the company sawed round logs into 4-sided cants on the sawmill and then cut cants into stringers and deck boards on the resaw. The boards from the resaw were then sent to a pallet notcher or trim saw and assembled into a new pallet.
Livengood Pallets continued recycling and manufacturing new pallets until market changes caused the company to revisit their business model. In the early 2010s, Jerry Livengood and his son Derek decided the best move for the company was to focus solely on recycling pallets and building combo pallets with both new and recycled material. “We got away from the core wars and started concentrating on uncommon sized pallets to dismantle and build the combo pallets,” said Jerry. “I wish we started building combos way before we did.”
Just weeks before Christmas in 2017, Livengood Pallets suffered a fire that burned their entire operation including a 6,000 square foot facility, pallet recycling equipment, and a large inventory of lumber. With the pallet plant shutdown, their employees found other jobs in order to make ends meet. During the next few months, Jerry and Derek rebuilt a new production facility and invested in a range of pallet recycling and manufacturing equipment including three Wood-Mizer Pallet Hawg dismantlers, trim saw, pallet notcher, and a semi-automated pallet assembly machine to get the business up and running again. “After the fire all my employees came back to work for us even though they had other jobs at the time,” said Jerry.
Today, the company operates with 8 full-time employees that do a range of jobs including transportation, machine operation, and material handling. Together, the team dismantles on average more than 700 pallets per day and manufactures a semi-load of 546 pallets per day. “Our pallets going out have 12 boards, and a lot of our pallets coming in only have 7 boards so that’s where the difference is to keep our daily flow,” said Jerry.
The centerpiece of the operation are two Wood-Mizer Pallet Hawg pallet dismantlers with a center drop and conveyor that automatically moves dismantled boards to the trim saw. “The Pallet Hawgs have very minimal maintenance and don’t lose power in the cut like the other machines we’ve used,” said Jerry. Each dismantler is operated by one person and dismantles upwards of 350 pallets per day per person. Compared to previous two-person dismantlers the company has used, the Pallet Hawg and conveyor system is achieving the same production with half of the operators. “One-man operation has been a lot better with less labor without less production,” said Jerry. “The conveyor system takes the lumber right to the trim saw so you don’t have to off load it. That’s one reason we went away from the two-man operation.”
Approximately 90% of pallets are sent to the dismantling line with two Pallet Hawgs and conveyor system while the remaining 10% are sent to a third Pallet Hawg dismantler with a rear drop and adjustable table height. With the pneumatic table lift, larger pallets from 8’ to 16’, pallets with bottom boards or solid decks, block pallets, and other specialty pallets are dismantled without difficulty. Having the third Pallet Hawg allows the flexibility to dismantle uncommon sized pallets without disrupting the production flow of common sized pallets on the first dismantling line. Due to lower RPM of each Pallet Hawg dismantler, Livengood Pallets has also experienced up to double the blade life compared to previous dismantlers they’ve ran. “A lot of the blade life depends on the type of pallets and operators, but we have a blade on right now that has six days on it,” said Jerry. “Three to five days is average, depending on the type of pallets and nails. With the previous machines we were lucky to get two days of blade life as the RPMs were twice as fast at 4500 RPM versus 2200 RPM of the Pallet Hawgs.”
After pallets are dismantled at one of the two lines, the deck boards are cut to length at the trim saw and stringers are notched at the pallet notcher. Finished deck boards and stringers are either stored in inventory or sent directly to the pallet assembly stations. “Our main pallet is the 48 inch by 40 inch GMA combo pallet which is primarily all we build,” said Jerry. “We try not to dismantle boards shorter than 36 inches, but when we do have shorter stock we generally build a 24 inch by 12 foot pallet or a custom-size to complete an order.”
By building relationships with local brokers as well as clients in the automobile and food storage industry, Livengood Pallets has standing orders which has helped with maintaining production flow. “We get most of our orders on Thursday and Friday for the following week so I can plan accordingly,” said Jerry. “We don’t have many last minute orders which has helped with our production planning.” For the future, Livengood Pallets has positioned themselves for continued growth and success in the pallet industry. “I owe a great deal of gratitude and a big thank you to our employees for the comeback of Livengood Pallet Service,” said Jerry.