Making End Grain Cutting Boards in Nova Scotia
By Ryan Moore, Wood-Mizer
Countries
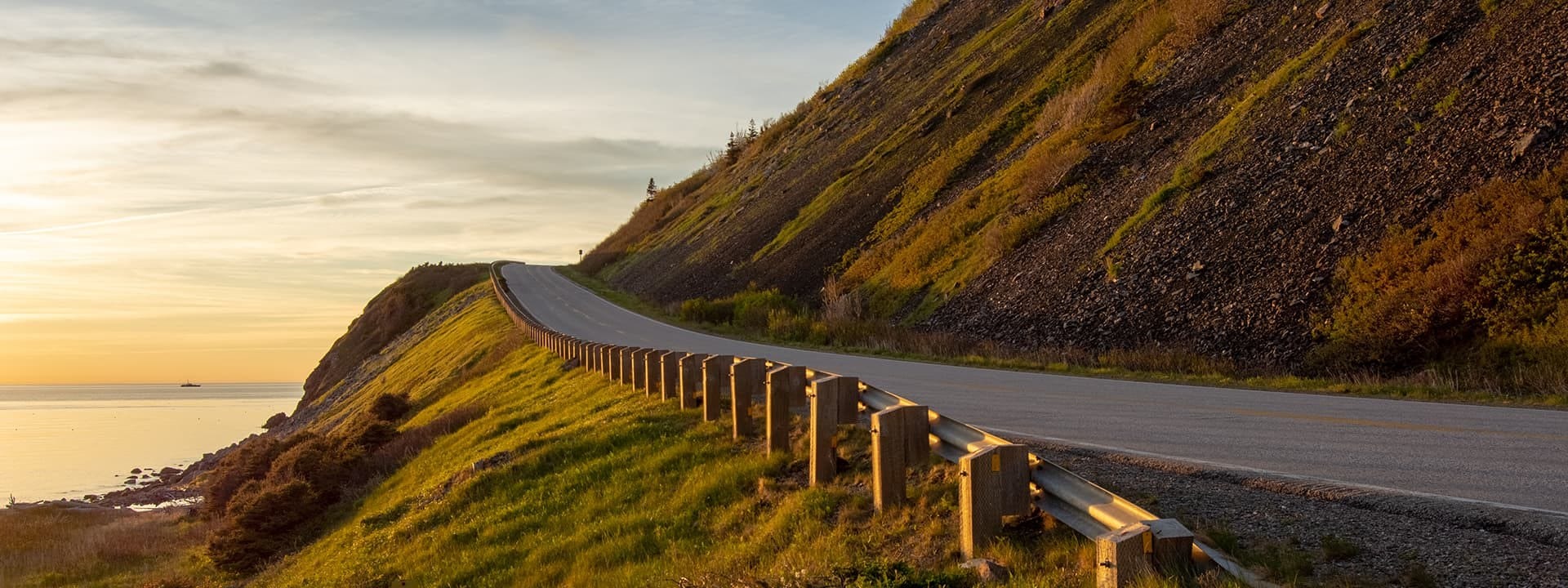
Located on Cape Breton Island in Nova Scotia, Canada, Larch Wood handcrafts wooden end grain cutting boards from sustainably managed and harvested larch trees. Don Beamish, General Manager of Larch Wood Canada designed these cutting boards in 2005 and took them to market. Cape Breton Island is the home of Cabot Trail, a scenic mountainside roadway and popular tourist destination for nature lovers. With the abundance of natural resources on the island, it is fitting that Larch Wood’s products take advantage of natural beauty with their unique end grain cutting boards. However, according to Don, there are more than just business reasons to enjoy living on Cape Breton Island. “It’s also just a wonderful place to live,” said Don. “The people are wonderful, the culture is wonderful. They have wonderful traditional music here as well.”
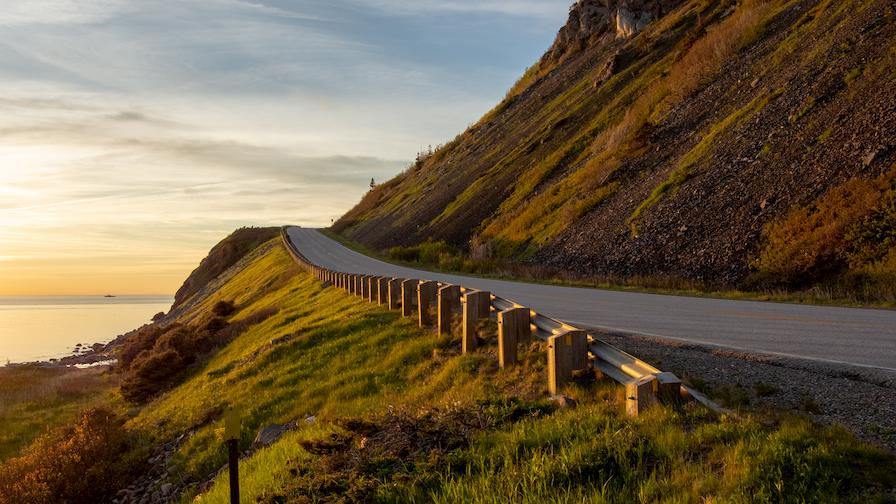
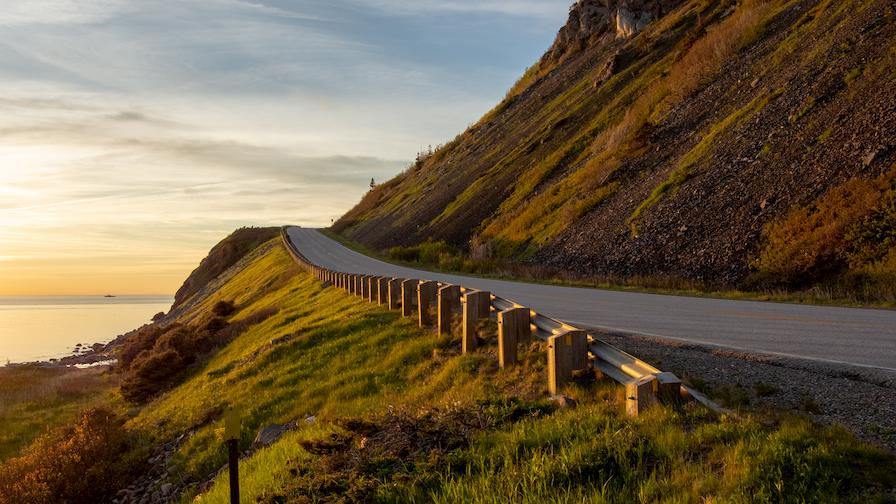
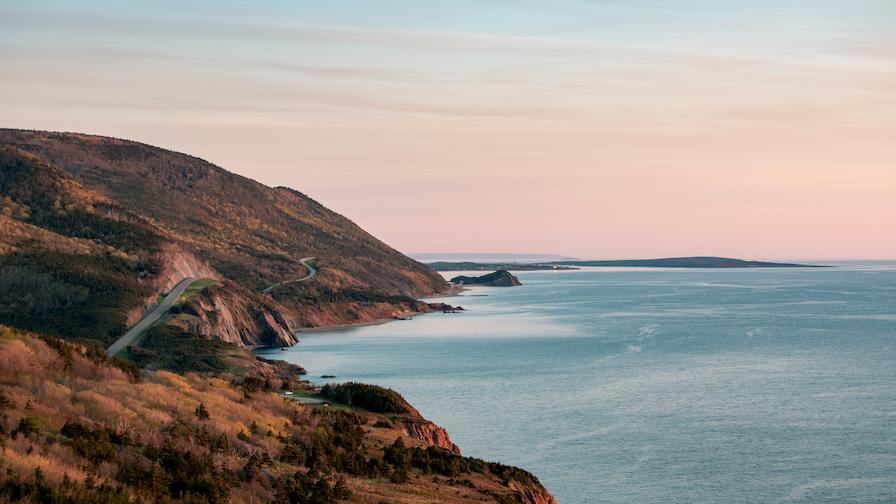
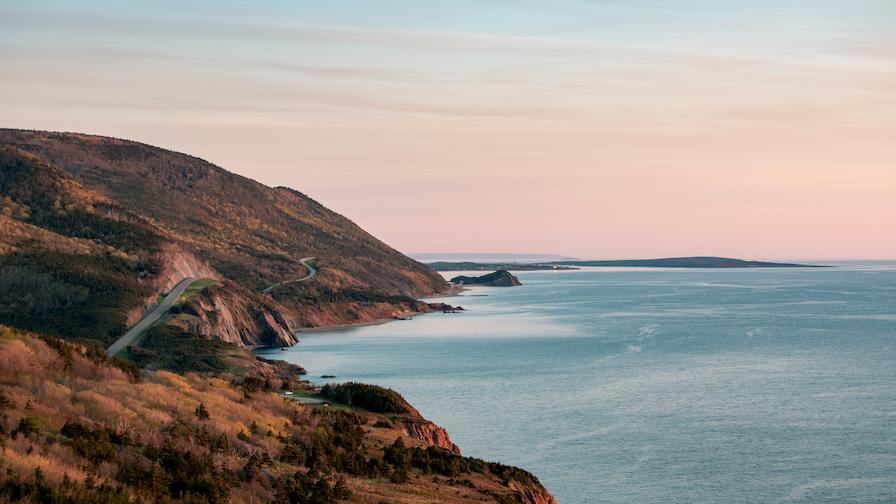
Larch Wood gets its name from the larch trees that are used to manufacture the cutting boards and cultivate the unique end grain patterns. Larch, or larix laricina, is a deciduous conifer meaning that it has needles but loses them in the winter, that can be commonly found in Canada and parts of the Northern United States. Larch Wood uses larch for their boards because of the beautiful, bold grain patterns that the wood can provide. Due to the variation of climate on Cape Breton, the larch trees on the island grow at a variety of different speeds, leading to different grain patterns. “Not only are they beautiful, but there’s a wonderful story to them,” said Don.
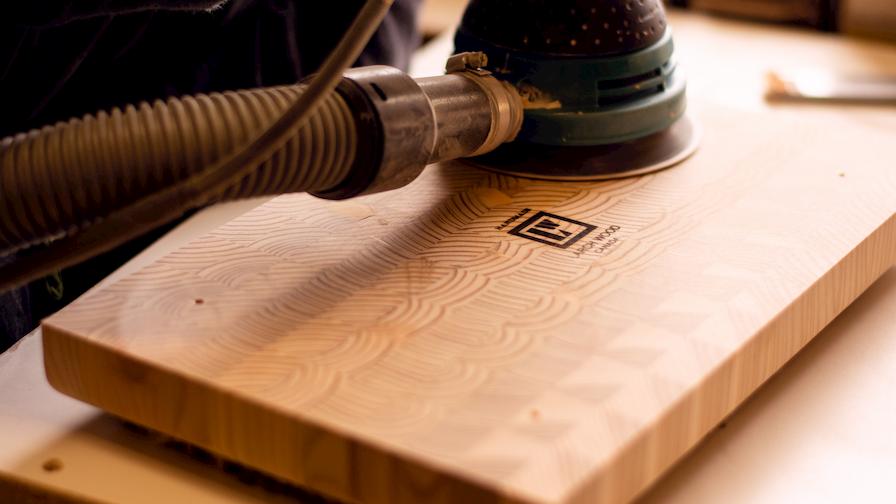
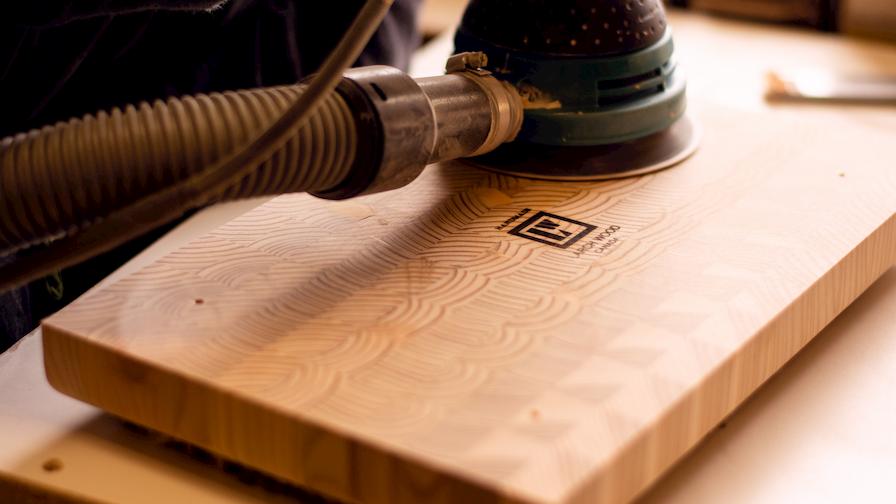
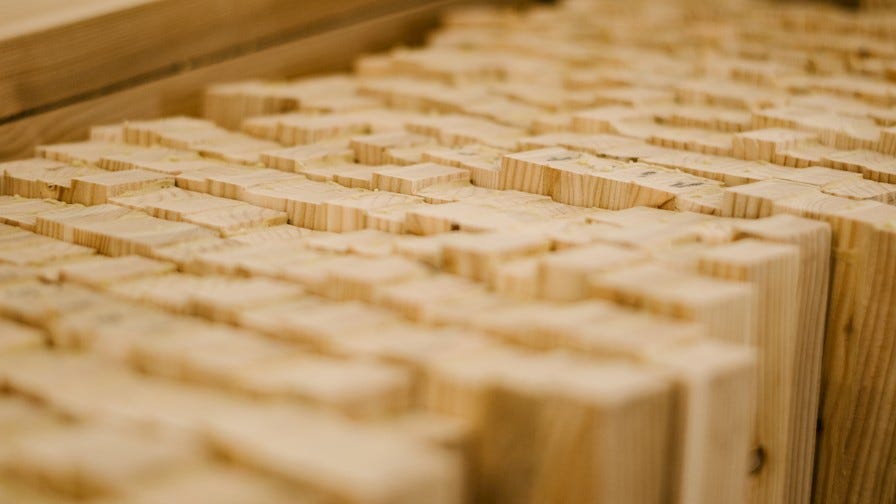
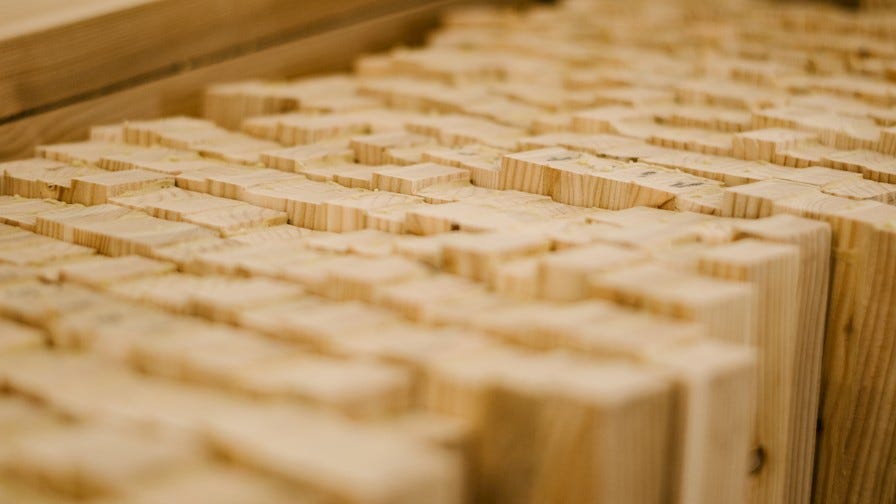
The end grain patterning is not only aesthetically pleasing but provides a practical benefit as well. Because the fibers in end grain are going vertical, they self-heal. When a knife hits the board, it separates the fibers in a way that allows them to pull back together. Due to this design, Larch Wood cutting boards are durable and can last generations. When Don first took his cutting boards to market, they were an instant hit. “I think the first show I took them to was in early 2005,” said Don. “People loved them, and we just ran with it.”
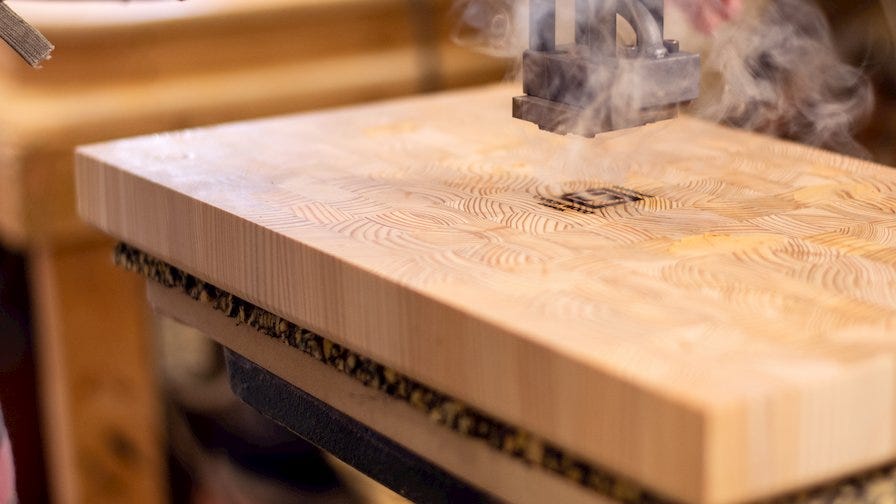
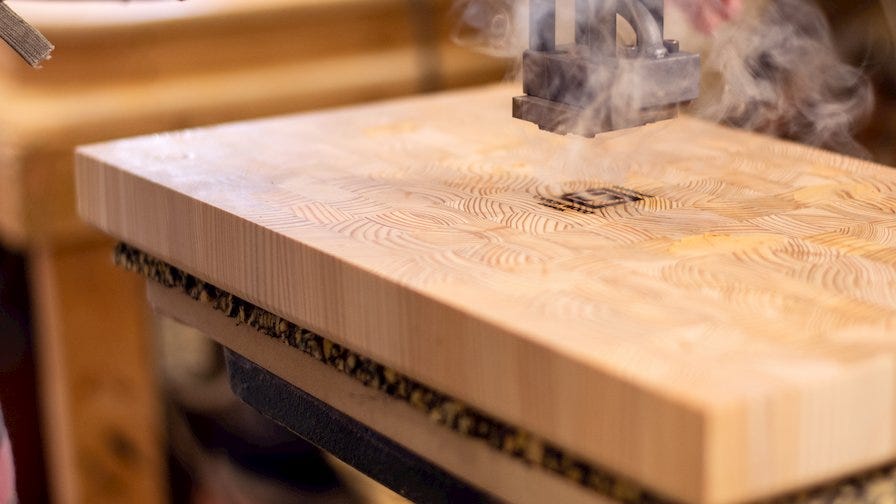
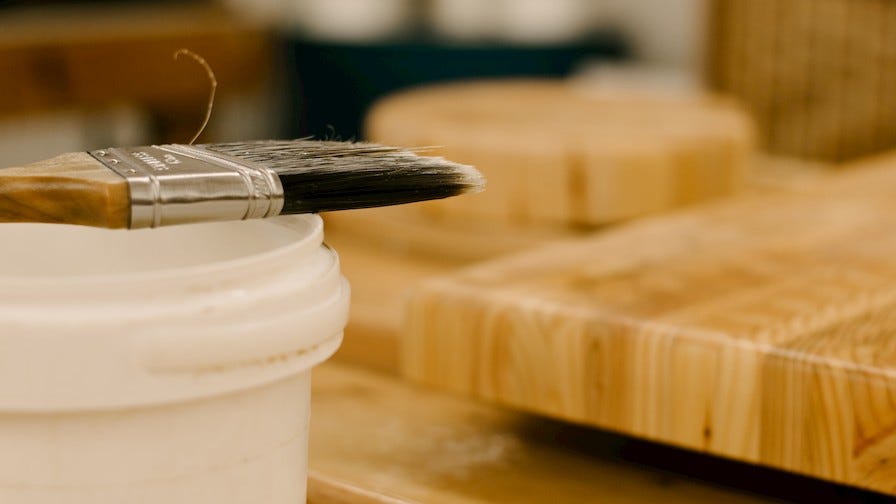
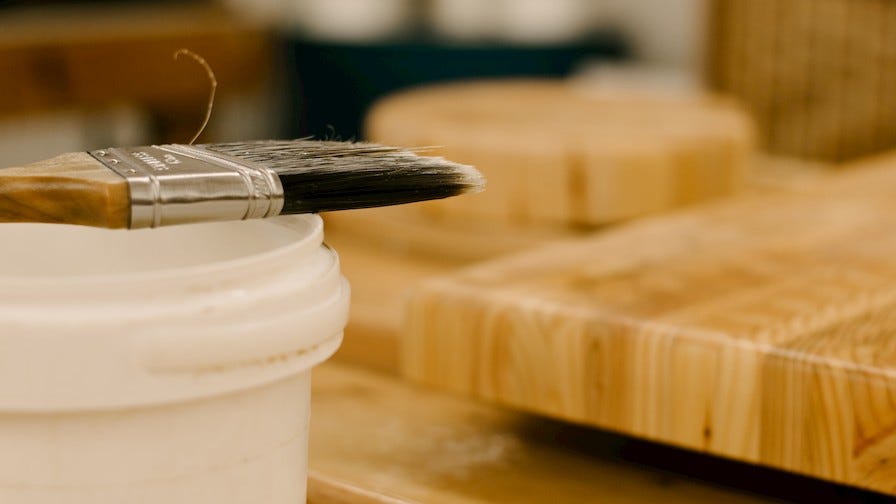
Larch Wood’s process for manufactured their cutting boards is very detailed. The first step for every Larch Wood cutting board is cutting larch logs into lumber. Larch Wood uses a Wood-Mizer LT40 Hydraulic portable sawmill to cut boards with precision and efficiency.
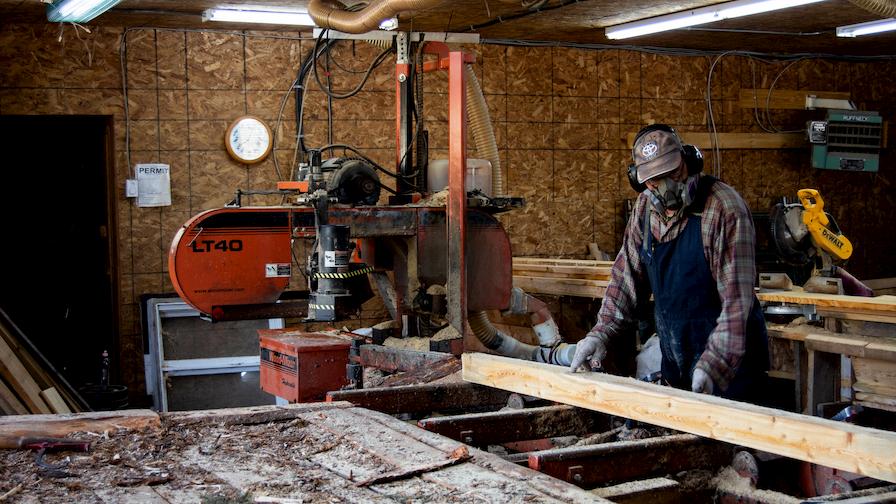
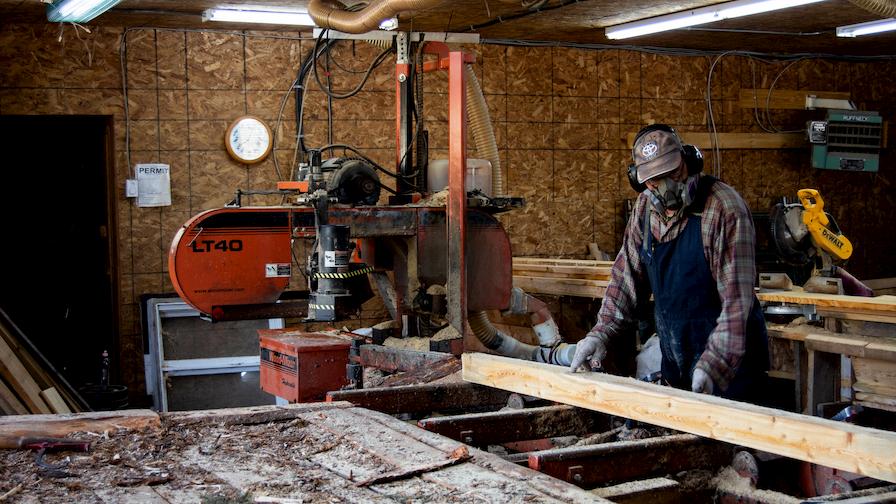
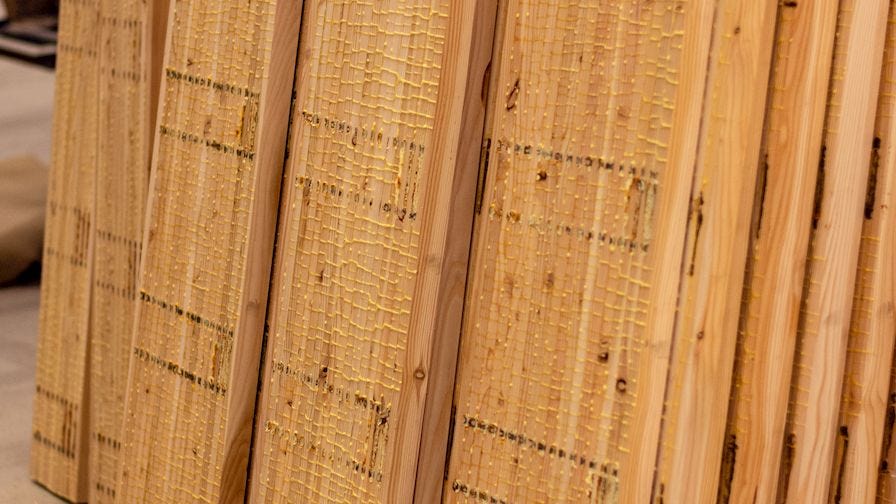
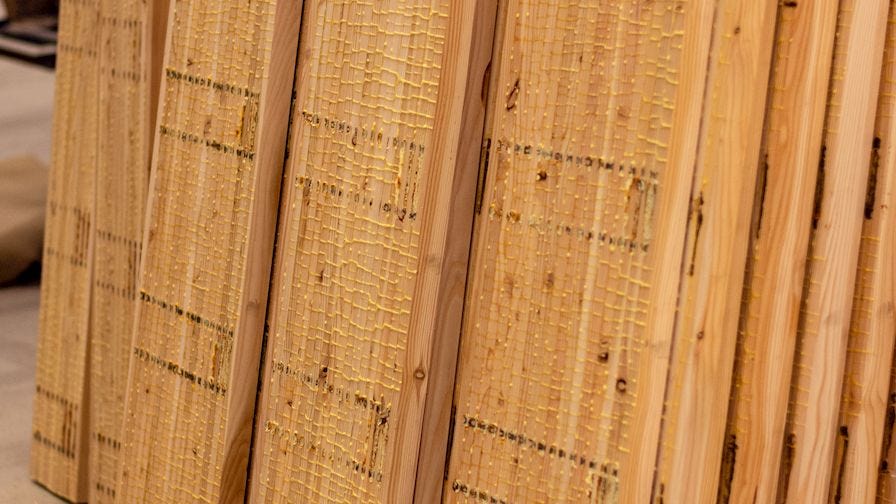
After leaving the sawmill, the timber is carefully stacked up and put into a wood kiln to dry. Dried timber goes to a cut-off saw where it is cut into different lengths. From the saw, material goes to the planer where it is planed on all four sides. The next step is a rip saw that cuts material into the required size for the final product. To make all boards exact dimensions, they pass through a moulder, to ensure that every board is perfect or identical in size.
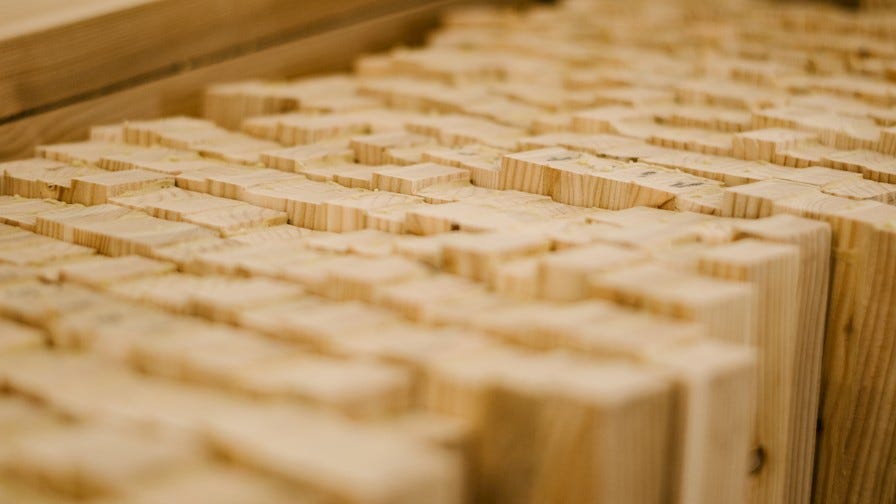
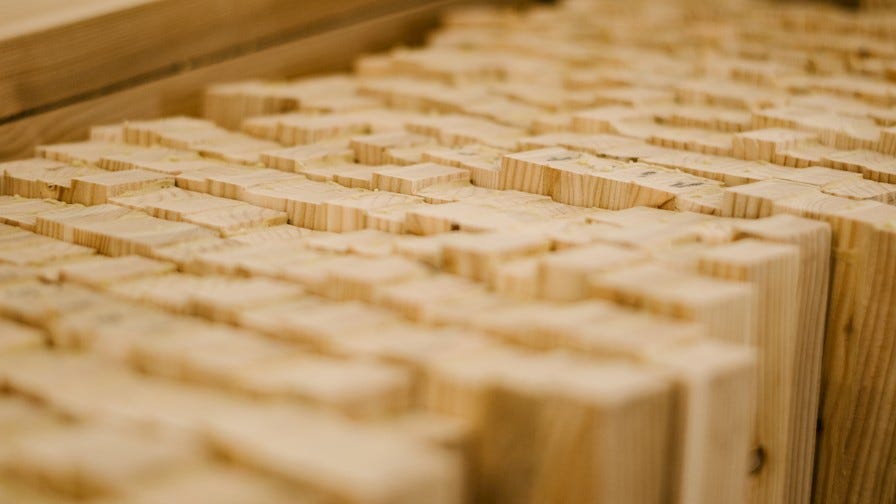
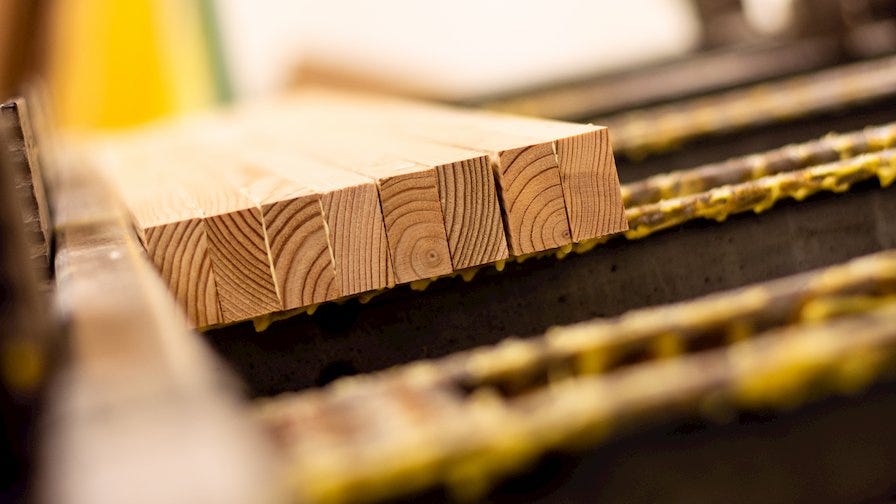
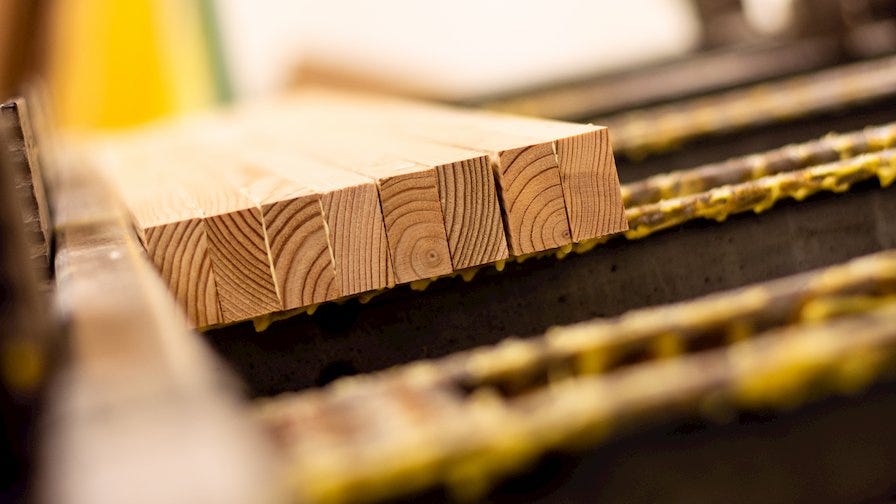
After that, it goes to a clamp carrier for the first gluing. "Guys that do that are looking on the ends of each stick to determine the pattern that's going to be on the final cutting board surface. They do a wonderful mix of grain patterns," said Don.
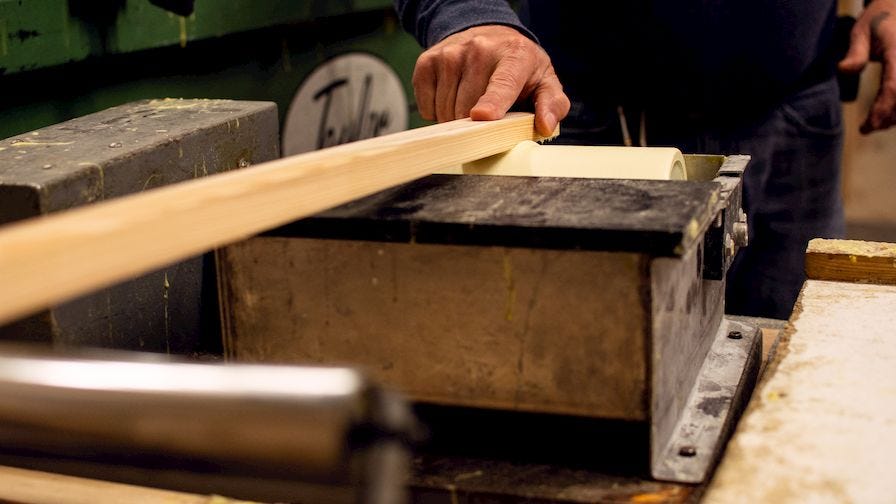
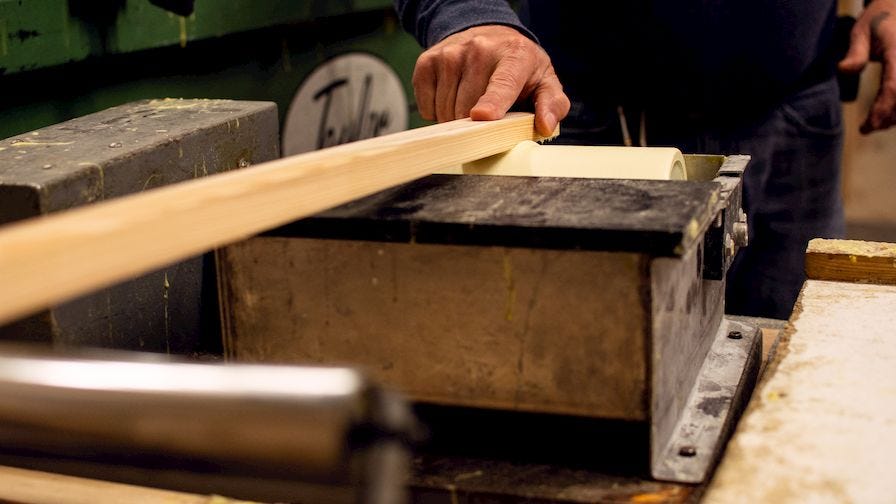
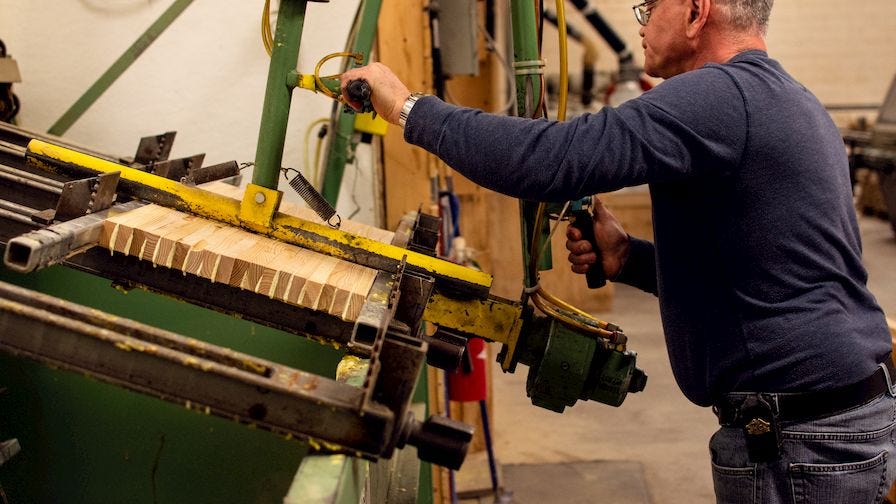
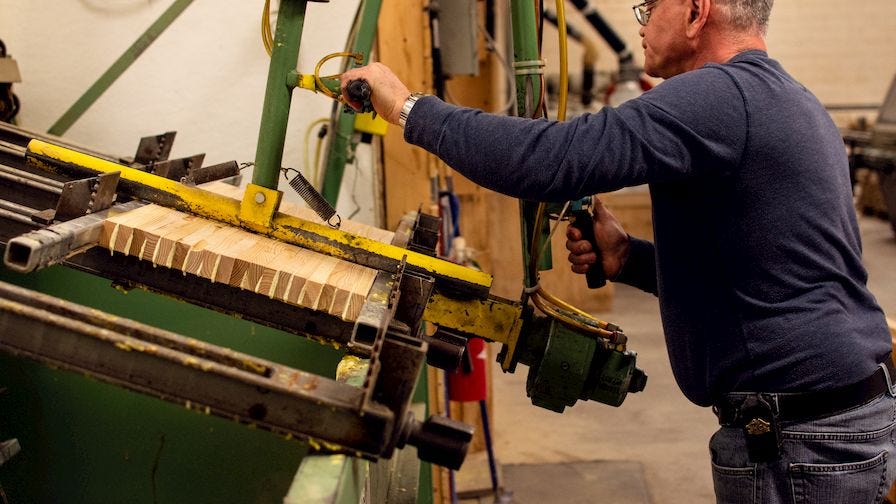
Once the gluing is finished, they are sent to the planer that removes the glue and makes the surface perfectly clean. From there they go to a table saw to be crosscut into two-inch sticks. These pieces are then passed to the second gluing. “Once that is done, you can actually see how boards are going to look like,” shared Don. Then they go through thickness sanders, finish sanders, and routing to round the edges. On the last step, the product is covered with three coats, two layers of mineral oil and one layer of wax, before they are packed to be shipped to customers.


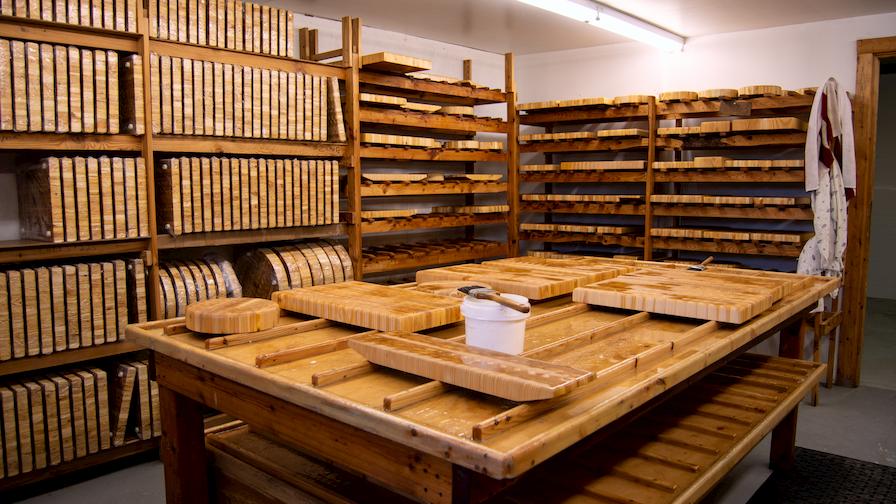
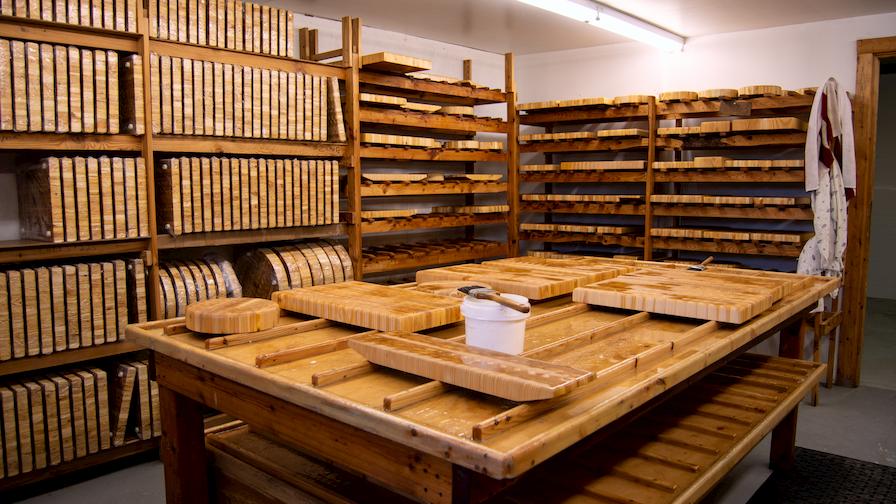


With the amount of care that is put into that manufacturing process, it is no surprise that Larch Wood’s cutting boards are unique, durable, and beautiful. “Our cutting boards are so unique I would say mainly because of the wood that we work with,” said Don. Larch Wood takes its larch all the way from the sawmill to ensure a high level of quality. “When you buy a board from us you should expect to end up with something that you are going to enjoy using, it’s going to be a focal point in your kitchen, and you’re going to be able to pass it on to your children,” said Don.
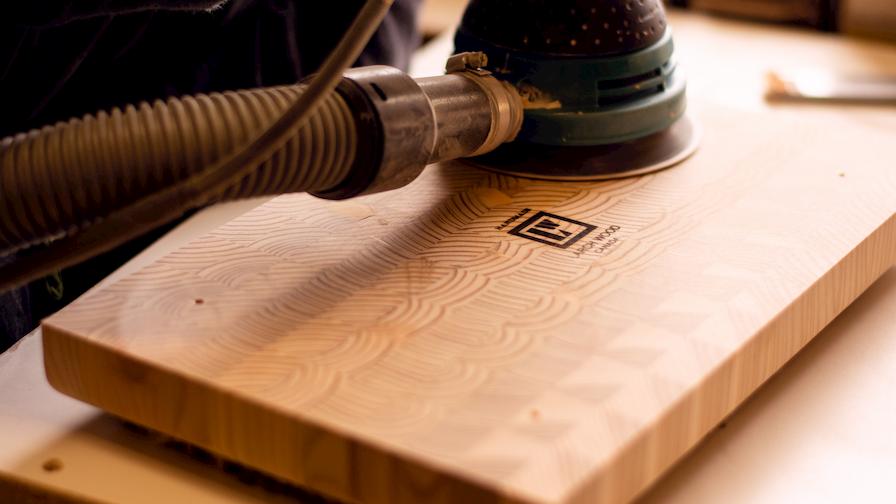
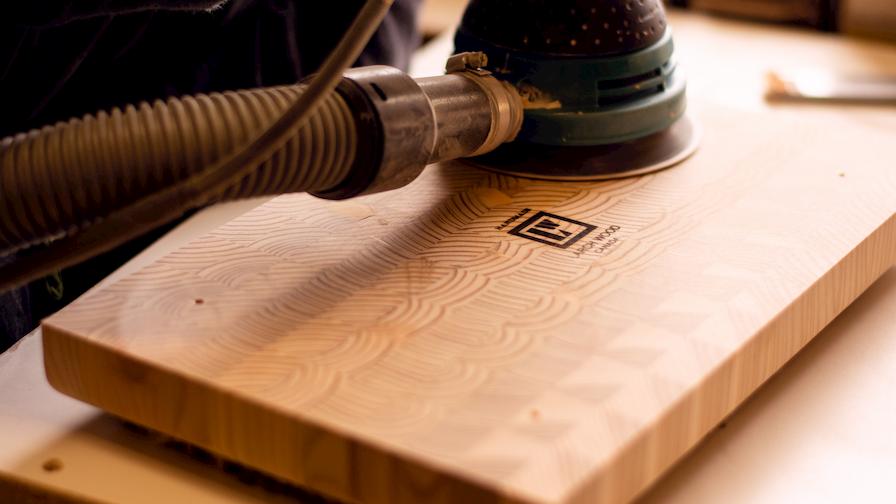
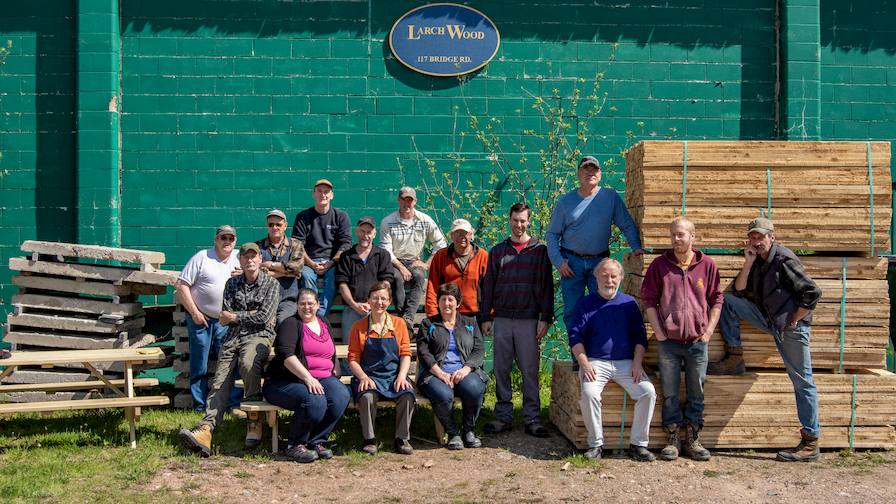
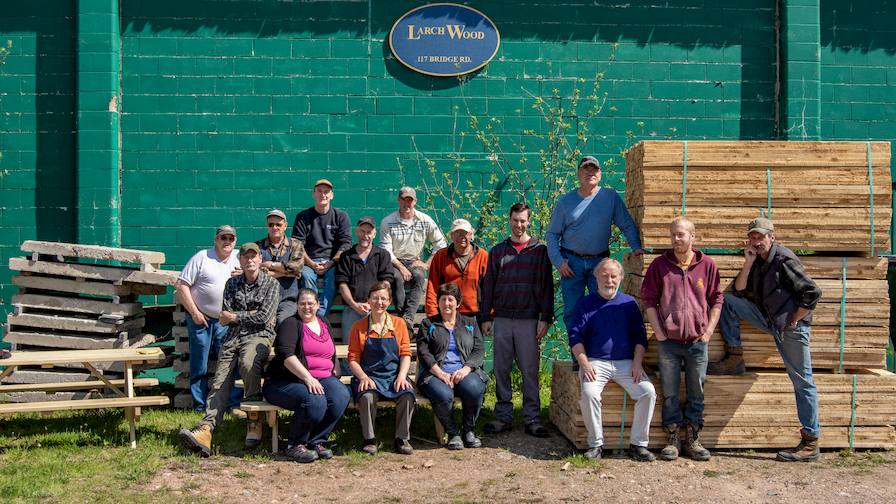
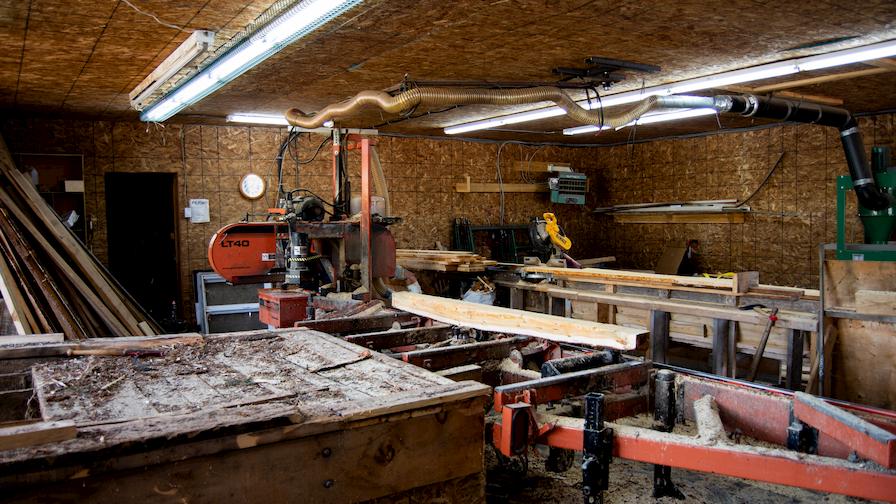
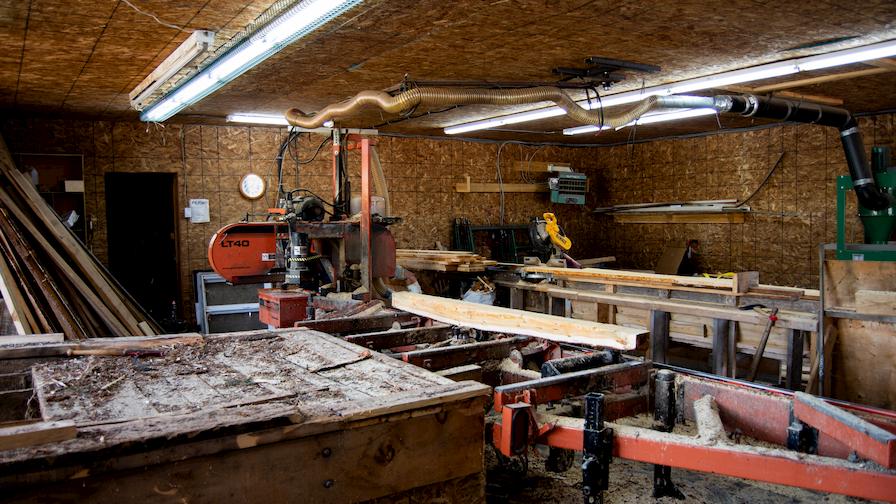
Located on Cape Breton Island in Nova Scotia, Canada, Larch Wood handcrafts wooden end grain cutting boards from sustainably managed and harvested larch trees. Don Beamish, General Manager of Larch Wood Canada designed these cutting boards in 2005 and took them to market. Cape Breton Island is the home of Cabot Trail, a scenic mountainside roadway and popular tourist destination for nature lovers. With the abundance of natural resources on the island, it is fitting that Larch Wood’s products take advantage of natural beauty with their unique end grain cutting boards. However, according to Don, there are more than just business reasons to enjoy living on Cape Breton Island. “It’s also just a wonderful place to live,” said Don. “The people are wonderful, the culture is wonderful. They have wonderful traditional music here as well.”
Larch Wood gets its name from the larch trees that are used to manufacture the cutting boards and cultivate the unique end grain patterns. Larch, or larix laricina, is a deciduous conifer meaning that it has needles but loses them in the winter, that can be commonly found in Canada and parts of the Northern United States. Larch Wood uses larch for their boards because of the beautiful, bold grain patterns that the wood can provide. Due to the variation of climate on Cape Breton, the larch trees on the island grow at a variety of different speeds, leading to different grain patterns. “Not only are they beautiful, but there’s a wonderful story to them,” said Don.
The end grain patterning is not only aesthetically pleasing but provides a practical benefit as well. Because the fibers in end grain are going vertical, they self-heal. When a knife hits the board, it separates the fibers in a way that allows them to pull back together. Due to this design, Larch Wood cutting boards are durable and can last generations. When Don first took his cutting boards to market, they were an instant hit. “I think the first show I took them to was in early 2005,” said Don. “People loved them, and we just ran with it.”
Larch Wood’s process for manufactured their cutting boards is very detailed. The first step for every Larch Wood cutting board is cutting larch logs into lumber. Larch Wood uses a Wood-Mizer LT40 Hydraulic portable sawmill to cut boards with precision and efficiency.
After leaving the sawmill, the timber is carefully stacked up and put into a wood kiln to dry. Dried timber goes to a cut-off saw where it is cut into different lengths. From the saw, material goes to the planer where it is planed on all four sides. The next step is a rip saw that cuts material into the required size for the final product. To make all boards exact dimensions, they pass through a moulder, to ensure that every board is perfect or identical in size.
After that, it goes to a clamp carrier for the first gluing. "Guys that do that are looking on the ends of each stick to determine the pattern that's going to be on the final cutting board surface. They do a wonderful mix of grain patterns," said Don.
Once the gluing is finished, they are sent to the planer that removes the glue and makes the surface perfectly clean. From there they go to a table saw to be crosscut into two-inch sticks. These pieces are then passed to the second gluing. “Once that is done, you can actually see how boards are going to look like,” shared Don. Then they go through thickness sanders, finish sanders, and routing to round the edges. On the last step, the product is covered with three coats, two layers of mineral oil and one layer of wax, before they are packed to be shipped to customers.
With the amount of care that is put into that manufacturing process, it is no surprise that Larch Wood’s cutting boards are unique, durable, and beautiful. “Our cutting boards are so unique I would say mainly because of the wood that we work with,” said Don. Larch Wood takes its larch all the way from the sawmill to ensure a high level of quality. “When you buy a board from us you should expect to end up with something that you are going to enjoy using, it’s going to be a focal point in your kitchen, and you’re going to be able to pass it on to your children,” said Don.